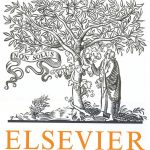
ترجمه مقاله نقش ضروری ارتباطات 6G با چشم انداز صنعت 4.0
- مبلغ: ۸۶,۰۰۰ تومان
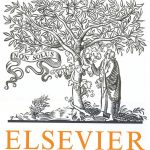
ترجمه مقاله پایداری توسعه شهری، تعدیل ساختار صنعتی و کارایی کاربری زمین
- مبلغ: ۹۱,۰۰۰ تومان
Abstract
Deviations during forging processes lead to workpiece failure when the forming limits of the material are exceeded. In production processes an early detection of manufacturing faults is preferred. The acoustic emission (AE) technique is examined with respect to its ability to detect deviations in lubrication conditions and in the structural integrity of different aluminum part geometries and alloys during forming. In a first step, an upsetting of varying specimen shapes was performed in order to study correlations of occurring defects as well as changing friction conditions with acoustic emission response. Afterwards, a cross joint was forged and AE was analyzed. The results suggest that crack detection during forging is feasible but limited by material ductility. In addition, it is shown that the characteristics of the acoustic emission during forming strongly depend on the respective alloy. With respect to faultless warm forging it is found that different stages are reflected in the AE signal, facilitating the detection of process deviations.
4. Conclusion
In this work,the potential ofthe AE technique for the detection of manufacturing faults and deviations during forging was examined for three different aluminum alloys. With respect to friction, there was merely weak evidence that deviations can be detected with the help of AE on the used test rig and AE acquisition setup. However, studies in lower frequency ranges and other surface dimensions or conditions are worth being performed in the future as a higher AE energy release might be possible in other cases. Further, it can be noted that the examined materials can exhibit very different AE characteristics. The alloy 5083 is susceptible to a PLC effect causing high AE activity. A high AE intensity could also be caused by fracture of inclusions in case of 7075. While up to a billettemperature of 150 8C the high-strength material 7075 allowed for an excellent crack detection for opening cracks in collar specimens, this was possible on 6082 only at room temperature. It can be concluded from the forging experiments that the application of the acoustic emission technique on processes with form elements is principally feasible, but its success strongly depends on the used alloy, state and temperature. It can be stated that the lower the ductility the higher the crack-related AE energy. The performed studies suggestthat cold forging has to be favored over warm or hot forging when the AE technique is considered for on-line crack detection. And even then it must be borne in mind that the ability of crack detection changes with the used material. A foregoing material characterization with simplified geometries is useful to examine this. As a main drawback for crack detection it should be mentioned that the guided flow of the material in real forging processes and the resulting local high strains and strain rates can impede the signal analysis due to overlaying deformation-related noise. Noise emitted by machines and environment is a further aspect to be considered. An evaluation of feature vectors can be a way to overcome such shortcomings. Finally, potential of identifying process deviations with respect to form filling in faultless warm forging operations was identified.