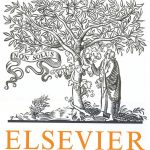
ترجمه مقاله نقش ضروری ارتباطات 6G با چشم انداز صنعت 4.0
- مبلغ: ۸۶,۰۰۰ تومان
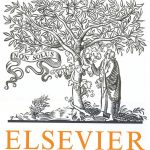
ترجمه مقاله پایداری توسعه شهری، تعدیل ساختار صنعتی و کارایی کاربری زمین
- مبلغ: ۹۱,۰۰۰ تومان
Abstract
The aim of this study is to investigate the design parameter effects of an aspirating cooling system on the outer surface temperature of a household pyrolytic oven glass. Pyrolytic ovens include complicated components, such as an oven door, a cross-flow fan and an aspirating cooling system, and their complex interactions should be investigated in detail. In this study, the oven door and cross flow fan and aspirating cooling systems were modeled as a three dimensional system using a computational fluid dynamics and heat transfer method to investigate the fluid flow and temperature distribution of outer surface of the oven door. The simulation model predicted the temperature distribution based on the cross flow fan speed, cross flow fan position and channel design of the aspirating cooling system. The numerical results were validated against results obtained from an experimental study. The computational results show that the rotational speed of the cross flow fan, the cross flow fan position and the channel design of the aspirating cooling system play important roles in affecting the outer surface temperature distribution of the oven glass of a pyrolytic oven.
5. Conclusions
The aim of this study was to investigate the heat transfer and fluid (air) flow characteristics of domestic ovens with aspirating cooling system (ACS) systems by implementing numerical methods. A prototype pyrolytic domestic oven was used. In the literature, numerical and experimental studies have been conducted for measuring the heat transfer and air flow inside oven cavities and within oven doors. The oven door and its upper fan provide active air suction from the door and were modeled using a computational fluid dynamic and heat transfer (CFDHT) method. The numerical results were validated by comparing with results obtained from experimental tests. In the literature, only a few studies have observed the heat transfer mechanisms of the oven door. A combined oven door and ACS was modeled in three dimensions, and parametric studies were performed. First, the ACS was modeled, and fluid flow was investigated. Based on these parametric studies, a new ACS model was developed with optimized CFF position and ACS channel geometry. After improving the ACS, the oven door and ACS were modeled together, and the outer surface temperature distribution of the oven door was investigated. Furthermore, the airflow Reynolds number was parametrically investigated. The computational results show that the designs of ACS channels, the CFF position and the rotational speed of CFF play important roles on the outer surface temperature distributions of the oven door and the flow fields of the ACS. These predictions are proven by experimental comparison of these models. The maximum temperature of the oven door decreased 65 K and the average temperature decreased 25.25 K in respect to the oven without ACS. These results shown that ACS can strongly reduce the surface temperature at the oven door which enables to design cool touch ovens even in the pyrolytic function where the inner temperature of the oven reach about 723 K.