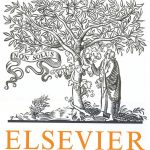
ترجمه مقاله نقش ضروری ارتباطات 6G با چشم انداز صنعت 4.0
- مبلغ: ۸۶,۰۰۰ تومان
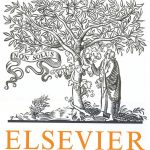
ترجمه مقاله پایداری توسعه شهری، تعدیل ساختار صنعتی و کارایی کاربری زمین
- مبلغ: ۹۱,۰۰۰ تومان
Abstract
Recent studies on improving the thermoelectric figure of merit (ZT) have advanced research into self-powered, wearable technologies using thermoelectric generators. However, previous design approaches do not consider structurally practical heat sink and module geometries, the use of a boost converter, or the size constraint of the generator due to aesthetic appeal, all of which lower the overall power output. Additionally, the reduced efficiency in using a boost converter changes the electrical and thermal load matching conditions for maximum power. In this study, the limitations of practicality were considered for a wearable thermoelectric generator that utilizes a state-of-the-art boost converter and an optimized heat sink. Heat sink fin geometries and thermoelectric module geometries were explored to maximize the power output within a 42.0 cm2 area and a 1.0 cm total height, in order to justify the wearability of the energy harvester. With optimized values of fin and module heights, the system was designed to produce 0.48 mW of electrical power at a boosted output voltage of 3.0 V, enough to power a small heart-rate monitor.
4. Conclusions
In designing an effective wearable thermoelectric generator, three practical issues of system integration must be considered: the limited heat dissipation from the cold side of the module, the low voltage reality of thermoelectric devices, and the overall size of the wearable device. Since a boost converter was used to increase the output voltage of the system, neither the traditional method nor the thermal load matching method could be used to optimize the generator. Furthermore, it was found that with the current materials and boost converters, practicality in design disallowed the optimum B-factor from being used, prohibiting the system from performing at its full potential and gaining its maximum power output. In designing the heat sink for the generator, the fin height was the dominating factor for reducing the generator’s cold size thermal resistance and providing the greatest output power. After optimizing a heat sink for natural convection and the module geometry within the practical constraints, a potential output of 0.48 mW at 3.0 V produced purely by body heat was calculated with the consideration of a boost converter for a thermoelectric generator with a total area of 42 cm2 and a total thickness of 1.0 cm. Due to its high output voltage, the thermoelectric generator was determined to be capable of powering small electrical devices. With known theoretical values, this paper calls for an experimental effort to build a prototype of a single link to provide experimental validation for the modeling results.