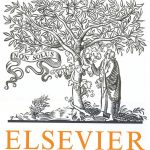
ترجمه مقاله نقش ضروری ارتباطات 6G با چشم انداز صنعت 4.0
- مبلغ: ۸۶,۰۰۰ تومان
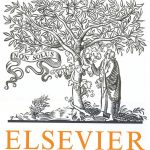
ترجمه مقاله پایداری توسعه شهری، تعدیل ساختار صنعتی و کارایی کاربری زمین
- مبلغ: ۹۱,۰۰۰ تومان
Abstract
There are precision issues with traditional rigid-body grippers due to their nature in presence of joints’ backlash and friction. This paper presents a macroscale compliant gripper to eliminate these issues for the applications in handing delicate/brittle materials such as powder granular or manipulating sub-millimetre objects such as optical fibre and micro-lens. The compliant gripper is obtained from a 2-PRRP (P: prismatic; R: revolute) kinematic mechanism, and uses distributed-compliance joints for avoiding stress-concentration and enabling large range of motion. A very compact design is achieved by using a position space principle. The compliant gripper is modelled, fabricated, followed by comprehensive testing for characterising relationships between the input displacement/force and output displacement and between the input displacement and displacement amplification ratio, and for analysing hysteresis during loading and unloading. The experimental results are compared with finite element analysis (FEA) model and linear analytical model. The testing results have suggested good performance characteristics of this compliant gripper such as a nearly linear relationship between the input and output, a nearly constant amplification ratio for closing the jaw, and negligible hysteresis error.
4. Conclusions
A compact and large-range compliant gripper has been designed, modelled and bi-directionally tested in this paper. Different from these existing solutions, the proposed design stems from a 2-PRRP kinematic mechanism by using distributed-compliance joints, with the consideration of the most compact design based on a position space principle. The testing results have shown some quantitative performance characteristics of this compliant gripper as follows: (a) A nearly linear relationship between the input force/ displacement and the output displacement; (b) A nearly constant amplification ratio, 1.3, especially for the extension testing case (i.e., closing the jaw); (c) A hysteresis error less than 2.5% for both the contraction and extension testing cases; (d) A 0.3 mm motion range for each jaw. The accurate analytical modelling, dynamic testing, control, and grasping testing are to be investigated following up the work in this paper. It is hoped that the miniaturised version of the compact compliant gripper can be fabricated in the near future. It is noted that the 2-PRRP mechanism can be used to design other compliant grippers when employing different compliant compositional modules with lumped and/ or distributed compliance.