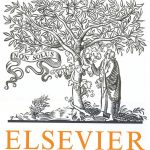
ترجمه مقاله نقش ضروری ارتباطات 6G با چشم انداز صنعت 4.0
- مبلغ: ۸۶,۰۰۰ تومان
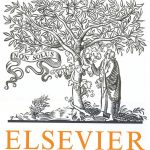
ترجمه مقاله پایداری توسعه شهری، تعدیل ساختار صنعتی و کارایی کاربری زمین
- مبلغ: ۹۱,۰۰۰ تومان
Abstract
Internal angles are used to strengthen Aircrafts center box corners where the wing is attached to the airframe. There are 16 angles in Airbus A300s wing box. On the right side, rear spur, and lower flange area of the center wing box, one of these angles had been cracked with a length of 28 mm. This crack has decreased residual strength of the part under allowed values and resulted to a rupture in the rear spur lower cap. Several reports of the same occurrences in other Airbus A300 air crafts, highlight the importance of finding the causes of this failure. Detailed optical and SEM, plus 4 other metallurgical tests were conducted on the failed angle. Finally, it was concluded that corrosion fatigue was the main reason which itself comes from manufacturing, maintenance, metallurgical, and geometric reasons as were discussed in this study.
12. Conclusion
According to failure investigation of the angle, corrosion-fatigue is apparently the main reason of the failure but there are some other obvious side reasons for this failure. – Surface corrosion is obviously cause of microscopic flaws in which very high values of stress intensities were created. So that, these flaws behave like initial cracks and become able to grow. – Incorrect or careless cold work maintenance job brought about scratches in the cracking region and is the second potential cause of cracking. – Existence of a filet at the vicinity of crack location created high values of stress intensity and stress concentration that can help crack propagation. Thus, part geometry is the third contributing factor of this failure.