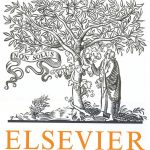
ترجمه مقاله نقش ضروری ارتباطات 6G با چشم انداز صنعت 4.0
- مبلغ: ۸۶,۰۰۰ تومان
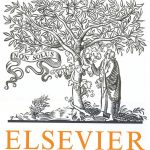
ترجمه مقاله پایداری توسعه شهری، تعدیل ساختار صنعتی و کارایی کاربری زمین
- مبلغ: ۹۱,۰۰۰ تومان
abstract
Being able to characterize the process signatures of powder bed based additive manufacturing process is key to improving the product quality. This paper demonstrates the implementation of a digital fringe projection technique to measure surface topography of the powder bed layers during the fabrication. We focus on developing the metrology tool and observing the types of information that can be extracted from such topographical data. The performance of the system is demonstrated with selected in situ measurements. Experimental results show this system is capable of measuring powder bed signatures including the powder layer flatness, surface texture, the average height drop of the fused regions, characteristic length scales on the surface, and splatter drop location and dimension.
4. Conclusion
Among all in situ measurement techniques reported to date, the surface topography of the powder bed and fused metal surface has not been widely investigated. An in situ fringe projection technique for LPBF has been developed to enable detailed layer-bylayer surface topography measurements with the goal of increasing our understanding of the process. The development of the system has been discussed in detail. The lateral and vertical measurement capability have been characterized using metrics called lateral point spacing and single point repeatability. In situ height maps have shown useful information about the fusion process, including the powder texture, fused region height variation, characteristic length scales on the surface, and average height drop of the fused regions. The results of this study indicate that fringe projection is a viable solution for in situ surface topography metrology. Implementation of this technique will help to further understanding of the LPBF process, and provide useful feedback for future close-loop process control.