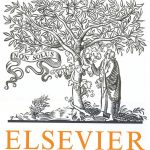
ترجمه مقاله نقش ضروری ارتباطات 6G با چشم انداز صنعت 4.0
- مبلغ: ۸۶,۰۰۰ تومان
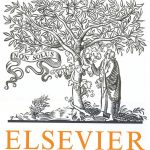
ترجمه مقاله پایداری توسعه شهری، تعدیل ساختار صنعتی و کارایی کاربری زمین
- مبلغ: ۹۱,۰۰۰ تومان
Abstract
The purpose of this paper is to report on an experimental study that explores the effect of using recycled rubber powder as an alternate fine aggregate in concrete mixes. Natural sand in the concrete mixes was partially replaced by 5%, 10%, 15%, and 20%. Physical properties such as the density, the compressive strength, the fresh concrete properties, the split-tension, and the impact load capacity are examined. The results revealed a decrease in the compressive strength of concrete cylinders containing rubber. The dynamic performance of the rubber concrete is of high importance because of its high resilient nature, as the rubber particles that are included in the concrete have a positive effect on the dynamic performance. The conclusions that were derived from this research implicate potential applications where rubberized concrete can be efficiently used. Even though rubberized concrete mixture generally has a reduced compressive strength that may limit its use in certain structural applications, it possesses a number of desirable properties, such as lower density, higher toughness, and higher impact resistance compared to conventional concrete.
VI. CONCLUSIONS
After extensively exploring this topic and studying different aspects of rubber concrete properties and behavior, a series of conclusions were derived:
1. Partial fine aggregates replacement in concrete mix by powdered rubber leads to a reduction in the density of the final product, because the specific gravity of rubber used was less than that of fine aggregates.
2. Decreasing in the rubberized concrete strength (compressive and tensile strength) with the increasing powdered rubber content in the mixture is always detected as shown in Figures 16 and 17. The strength reduction may be attributed to two reasons. First, because the rubber particles are much softer (elastically deformable) than the surrounding mineral materials, and on loading, cracks are initiated quickly around the rubber particles in the mix, which accelerates the failure of the rubber–cement matrix. Second, soft rubber particles may behave as voids in the concrete matrix, due to the lack of adhesion between the rubber particles and the cement paste.
3. For a design mix strength ranging between 30 MPa and 50 MPa, the reduction in the compressive strength is consistent and almost at a constant ratio with the increase in the percent of powdered rubber. The reduction in strength is an average of 30, 35, 50, and 63 % against a powdered rubber replacement of fine aggregates at 5, 10, 15, and 20 %, respectively.