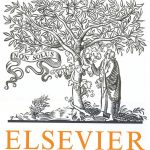
ترجمه مقاله نقش ضروری ارتباطات 6G با چشم انداز صنعت 4.0
- مبلغ: ۸۶,۰۰۰ تومان
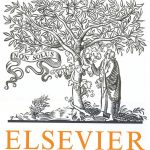
ترجمه مقاله پایداری توسعه شهری، تعدیل ساختار صنعتی و کارایی کاربری زمین
- مبلغ: ۹۱,۰۰۰ تومان
Abstract
Continuous carbon nanotube (CNT) yarn filaments can be employed as an inherently multifunctional feedstock for additive manufacturing (AM). With this material, it becomes possible to use a single material to impart multiple functionalities in components and take advantage of the tailorability offered by fused filament fabrication (FFF) over conventional fabrication techniques. Some of the challenges associated with coupling this emerging material with advanced processing are addressed here through the fabrication and characterization of additively manufactured functional objects. Continuous CNT yarn reinforced Ultem® specimens are characterized to determine their mechanical and electrical properties. The potential to produce net shape fabricated multifunctional components is demonstrated by additively manufacturing a quadcopter frame using Ultem® and continuous CNT yarn reinforced Ultem®, where the CNT yarn reinforcement was designed to also act as the electrical conductors carrying current to the motors.
4. Summary and conclusions
Multifunctionality in a 3D printed part was demonstrated by utilizing CNT yarn filament and a thermoplastic polymer. Developments undertaken to permit FFF of Ultem® and CNT yarn filaments on an open-source printer were described. Approaches to overcome challenges associated with printing continuously reinforced components that were presented here include: a. development of a printable CNT yarn filament with a high performance polymer matrix, b. development of the printing method yielding accurately placed, sufficiently adhered CNT yarn filament so measureable improvements in mechanical properties confirm structural reinforcement c. a simple cutting mechanism that permitted the termination of CNT yarn filament as needed at the point of deposition and automated initiation of the next print step. Successful implementation of the above methods on an inexpensive open-source printer was confirmed by determining the performance characteristics of the printed parts. Components were evaluated to demonstrate the mechanical property enhancement afforded by reinforcing Ultem® with CNT yarn and the added functionalities enabled by this structural reinforcement due to its electrical properties. Retention of the electrical conductivity in the CNT yarn filament allowed electrical components (wiring, heating elements and strain sensors) to be built directly into the structure of the 3D printed parts. Since CNT yarns are strong, electrically conductive, and highly flexible, strain gauges embedded into a part can act in both structural reinforcement and sensing capacities. The printed quadcopter showcases the potential to fabricate multifunctional, tailored components that take advantage of the suite of properties offered by CNT yarns.