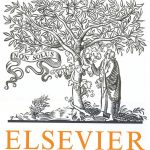
ترجمه مقاله نقش ضروری ارتباطات 6G با چشم انداز صنعت 4.0
- مبلغ: ۸۶,۰۰۰ تومان
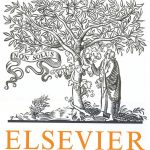
ترجمه مقاله پایداری توسعه شهری، تعدیل ساختار صنعتی و کارایی کاربری زمین
- مبلغ: ۹۱,۰۰۰ تومان
abstract
Carbon fibre reinforced polymer (CFRP) externally bonding is an efficient and effective method to strengthen damaged steel beams, and thereby prolong their service life. However, debonding failure, which requires accurate predictions to ensure safety, can occur before the full usage of CFRP. In this study, the notched steel beams strengthened with CFRP plate were simulated by finite element method where the mixed-mode cohesive law was employed to determine the interfacial stress. The load–deflection curves and strain development at different load levels from experimental study were used to verify the validity of the numerical model. The interfacial stress distribution with increasing load was analysed, and good correlation with theoretical calculations at elastic stage was observed. In contrast to the previous elastic analytical study, the plastic behaviour of the CFRP strengthened notched steel beams was revealed. More importantly, interfacial crack initiation, propagation and debonding were accurately simulated. This simulation method can be used to predict debonding process in actual engineering applications. In addition, parametric analysis was conducted to assess the effects of notch depth, CFRP elastic modulus and CFRP thickness. The ultimate load and ductility decreased substantially with increasing notch depth. Furthermore, although increased bearing capacity was achieved by increasing the CFRP elastic modulus and thickness, ductility decreased and premature debonding failure occurred more easily.
7. Conclusions
In this paper, the mixed-mode cohesive law was applied to simulate notched steel beams strengthened by CFRP plates, and authors’ theoretical and experimental results were compared for model verification. As discussed, the following conclusions can be made. (1) The mixed-mode cohesive law was validated by the experimental results as an effective model for simulating the mechanical behaviour of notched steel beams strengthened by CFRP plates. Compared with the average debonding and ultimate loads from test and FEM results, the deviations are about 6.0% and 5.4%, respectively. The accuracy of the model is also demonstrated by the load-deflection curves and the strain distributions at the debonding load and ultimate load. (2) The debonding process of notched steel beams strengthened with CFRP plates can be accurately simulated by the numerical model. How the longitudinal shear stress and normal stress change with increasing load is clear from the simulated results. The simulation tool is important for the development of debonding prevention measures and improvement of the bearing capacity. (3) The simulated results agree with the theoretical results for specimens in the elastic stage. However, the difference becomes obvious in the plastic stage, which implies that the results from the theoretical calculation were overestimated. For better accuracy and safety, in engineering applications, it is necessary to predict the debonding and ultimate loads of specimens using numerical models.