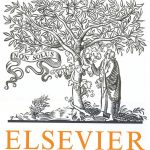
ترجمه مقاله نقش ضروری ارتباطات 6G با چشم انداز صنعت 4.0
- مبلغ: ۸۶,۰۰۰ تومان
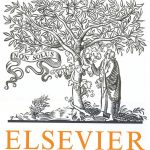
ترجمه مقاله پایداری توسعه شهری، تعدیل ساختار صنعتی و کارایی کاربری زمین
- مبلغ: ۹۱,۰۰۰ تومان
Abstract
We are witnessing the emergence of a new paradigm in the modeling of material structures. It stems from the digitization of manufacturing and is fueled by advances in additive manufacturing and material science. This paper strives to provide a critical examination of this new paradigm in a historical and technological context and to show that it requires non-trivial extensions and generalizations of the classical theoretical foundation and algorithmic solutions originally developed for solid modeling. Specifically, it requires new models and data-intensive representations for materials, physical behavior, and manufacturing processes across multiple scales. In particular, we argue that most computational tasks that support traditional and emerging manufacturing may be formulated systematically and addressed in terms of relations (conversions, synthesis, change propagation updates, verification, and other harmonization activities) among four views (manifestations) of an engineered artifact: Functional, which captures the design constraints and tolerances on shape, properties, and behavior; Designed, which represents a toleranced design that satisfies these constraints; Planned, which defines a manufacturing process plan; Simulated, which models the expected outcome of the process plan; and a Real sample set of physical artifacts produced by executing the process plan on a particular manufacturing technology. Based on this formulation, we outline important directions for a research agenda aimed at enabling, driving, and amplifying further advances in digital design and manufacturing
5.3. Standardization and interoperability
Based on our experience with traditional solid modeling, issues related to standardization and interoperability of models, representations, and systems are likely to emerge as more critical bottlenecks than the modeling technology itself. The importance of interoperability in modeling of material structures was also highlighted in panel discussions at recent manufacturing conferences [50]. Broadly, interoperability refers to ability to convert, harmonize, and combine distinct computer representations of material structures between two different views. Theoretically, standardization and interoperability of different representations of material structures will require a broad agreement on a common formal reference model of what such structures are mathematically. Such an agreement may be difficult or impossible to achieve, given the richness and complexity of the four representations discussed above. Geometric models and representations are relatively well understood in the context of solid modeling [5,11], and recent proposals for material models include combinatorial models extending geometric complexes to cochains complexes [51], point set models extending manifolds to fiber bundles [52], as well as more pragmatic approaches extending implicit models to material property fields [53], and replacing commonly used STL format by a more general AMF format [29] that supports curved geometry and some material information. However, the issue of what constitutes a suitable formal model of materials, physical behavior, processes, scale and uncertainly remains largely open.