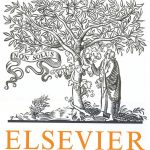
ترجمه مقاله نقش ضروری ارتباطات 6G با چشم انداز صنعت 4.0
- مبلغ: ۸۶,۰۰۰ تومان
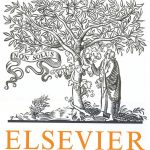
ترجمه مقاله پایداری توسعه شهری، تعدیل ساختار صنعتی و کارایی کاربری زمین
- مبلغ: ۹۱,۰۰۰ تومان
abstract
Tyre bead grade wire is used for tyre making application. The wire is used as reinforcement inside the polymer of tyre. The wire is available in different size/section such as 1.6– 0.80 mm thin Cu coated wire. During tyre making operation at tyre manufacturer company, wire failed frequently. In this present study, different broken/defective wire samples were collected from wire mill for detailed investigation of the defect. The natures of the defects were localized and similar in nature. The fracture surface was of finger nail type. Crow feet like defects including button like surface abnormalities were also observed on the broken wire samples. The defect was studied at different directions under microscope. Different advanced metallographic techniques have been used for detail investigation. The analysis revealed that, white layer of surface martensite was formed and it caused the final breakage of wire. In this present study we have also discussed about the possible reason for the formation of such kind of surface martensite (hard-phase).
5. Discussions
Premature wire failures were observed during bending operation before tyre making process. The nature of the defects was of similar type in all the failed samples. The fracture surface was of finger nail type. Crow feet like defects including button like surface abnormalities were observed on the broken wire samples. The surface defect was observed near the fracture end and in localized manner. Etched microstructure of the longitudinal samples revealed presence of brown layer near the defectlocation. The thickness ofthe brown layer is around 30–40mm. From microstructure analysis the brown layer appeared to be of martensite (which was further verified by micro hardness value and SEM analysis). Severe grain flow was observed along the defect location. The microstructure of the matrix revealed cold drawn pearlite structure. The average hardness of the matrix is about 460 HV, and the average hardness value of the brown phase is around 650 HV. This type of layer is generated during wire drawing due to lack of lubrication as no segregation was observed [4]. The martensite layer which forms a brown layer in the surface is very brittle in nature (high hardness). This surface martensite helps to propagate cracks from the pearlite–martensite interface and which leads to failure during drawing or its successive operations. The martensite formed in the surface is a thermal phenomenon generated during friction causes surface temperature rise followed by rapid cooling due to mass effect of bulk. EDS analysis reveals presence of tungsten (W) in the martensite region in concentration of more than 2% as the element is not contained in bulk, which indicates that the materialtransfers between the mating bodies i.e. an intense adhesive sliding wear. The martensite formed in the surface was generated during drawing process probably due to lack of localize lubrication [5]. Due to improper lubrication, during drawing of high carbon wires sometimes temperature reaches up to austenitic range due to heat generated, because of plastic deformation and friction between wire and die [6].