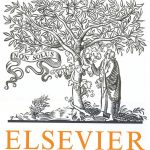
ترجمه مقاله نقش ضروری ارتباطات 6G با چشم انداز صنعت 4.0
- مبلغ: ۸۶,۰۰۰ تومان
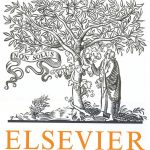
ترجمه مقاله پایداری توسعه شهری، تعدیل ساختار صنعتی و کارایی کاربری زمین
- مبلغ: ۹۱,۰۰۰ تومان
5. Conclusion
In this work, we introduce a non-uniform regularization technique for variational shape deformation. We use diffusionbased techniques to generate a smooth scalar field and users are allowed to control the magnitude and range of the regularization. With our technique, it is possible to interactively control the deformation with no noticeable discontinuity artifacts, while the global shape distortion is kept lower. We extend the traditional regularization techniques to bring more flexible control of the regularizer. The flexibility is at the price that users are required to adjust more parameters. An interesting direction for future work is to automatically select parameters for any specified deformation. We approximate the diffusion equation with one linear equation in this work, which does not produce the exact solution on shapes. It is still worth studying how to efficiently solve the diffused weights with higher precision. Besides, our method works under the assumption that the smoothness of the distortion map around control points well follows the diffusion model. There is no theoretical guarantee about this assumption and it is essential to continue a theoretical study to model the discontinuity artifacts. In addition, since bijectivity is not explicitly modeled as a hard constraint in the deformation energy or the regularizer, the regularized deformation is not guaranteed to be bijective even if a strong quadratic regularizer is applied. We will keep exploring effective regularization techniques to suppress the inverted elements under extreme deformation.
6. Conclusion
In this paper, the minimum void length scale control is well addressed under the level set framework. Innovatively, two lower bounds are concurrently applied which correspond to the different machining tool radii of the rough-to-finish machining process. The derived optimal design demonstrates the outstanding characteristics that, both rough and finish machining operations can be effectively performed, through which both the machining efficiency and quality can be guaranteed. As for the side effects, the applied double lower bounds slightly sacrifice the design optimality. Especially for the rough machining lower bound, if a large value is applied, the optimal structural topology may not be achievable. For further work, we intent to extend the developed minimum void length scale control method to address stress-constrained problems, which is even more challenging because the stress level is not simply monotonic to the material volume fraction.