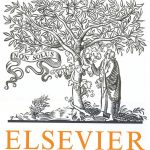
ترجمه مقاله نقش ضروری ارتباطات 6G با چشم انداز صنعت 4.0
- مبلغ: ۸۶,۰۰۰ تومان
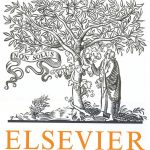
ترجمه مقاله پایداری توسعه شهری، تعدیل ساختار صنعتی و کارایی کاربری زمین
- مبلغ: ۹۱,۰۰۰ تومان
abstract
Wind turbine technology is experiencing rapid growth with respect to size, market share, and technological design. Operational and maintenance cost directly determine whether the system is efficient in terms of energy production in comparison with other types of power plants. Condition monitoring of wind turbines is the major field of studies in recent years aiming to increase lifetime expectancy of components while reducing operation and maintenance cost. Operators and researchers are focusing on improving fault detection techniques in order to render wind turbines more reliable. Gearbox in wind turbines has the greatest share of downtime among all other components affecting directly the cost of operation and maintenance. This paper gathers a review on different methods and techniques for gearbox condition monitoring in wind turbines. Furthermore, various methods and techniques in the literature will be presented in order to get an insight onto the most used methods in wind turbine gearbox condition monitoring. Challenges and future aims are also discussed to determine the focus of condition monitoring systems.
Discussion and conclusion
Condition monitoring of wind turbines is an evolving field. Operators, researchers, and nations are highly focusing on improving wind turbine efficiency as a reliable replacement for the old polluting fossil fuel based electricity plants or dangerous nuclear plants. In order to reach an efficient system, it is vital to increase the lifetime expectancy of each component. Gearboxes cause a great share of the downtime of wind turbines when a fault occurs. Condition monitoring of gearboxes can be done through numerous and various approaches and techniques. Lubrication analysis is still the hardest to be applied since it relies on oil sample analysis or sensory systems. Oil sample analysis is done offline and might detect faults when it is too late. Moreover, sensory systems for debris detection are costly and require maintenance. On the other hand, several lubricant parameters can be indicators either for lubricant degradation (viscosity, humidity, etc.), or component failure (debris). The challenge in lubrication analysis come down to well chosen monitored parameters and the set of sensors to be installed responsible to monitor these parameters. Acoustic Emission analysis has been employed in all mechanical rotating systems. It is capable of detecting faults and lately localizing them. Since AE analysis deals with signals of high frequency, it is seen that signal processing techniques are used to extract signal features for gearbox fault detection in wind turbines. The main important and tedious challenge when using AE resides in the isolation of noises. Background internal and external noises interference may well render signal analysis useless for fault feature detection.