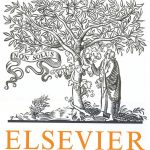
ترجمه مقاله نقش ضروری ارتباطات 6G با چشم انداز صنعت 4.0
- مبلغ: ۸۶,۰۰۰ تومان
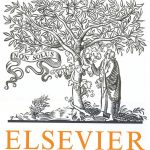
ترجمه مقاله پایداری توسعه شهری، تعدیل ساختار صنعتی و کارایی کاربری زمین
- مبلغ: ۹۱,۰۰۰ تومان
Abstract
This study presents a failure analysis of a femoral orthopedic implant. This implant is a locking compression plate that was fixed to a broken femur using two types of screws: locking and compression screws. The study elucidates the causes of an in situ premature failure of the plate and screws. Chemical analysis, hardness tests, and microstructural analysis confirmed that the implant was manufactured from cold-worked stainless steel 316L. The macro and micro fractographic analyses revealed that the failure mechanism was high-cycle fatigue and that the implant underwent approximately 106 loading cycles before failure. A finite element analysis of the assembly indicated that the crack initiation sites are located in the region where the highest stresses are observed. This numerical analysis confirmed that walking induces the loading condition needed for this specific failure. According to this loading condition and to the material properties, the stress amplitude that initiated and propagated the crack is estimated to be in the range of 400 MPa. Several considerations, both mechanical and medical, are discussed in order to explain the failure and to improve the system durability. From an engineering perspective, implant geometry and installation procedure could be optimized in order to reduce the stress concentrations that developed near the crack origin.
8. Conclusion and recommendations
The present work allowed describing the complex fatigue failure of a bone-LCP assembly. According to a finite element analysis and to an estimation of the number of fatigue cycles, walking was enough to induce fatigue damages. The stress variation needed to initiate and propagate the fatigue cracks within the screws and the implant were estimated to be in the range of 400 MPa at R = 0. The implant geometry and the uncontrolled preload are possible causes of stress concentration. Nevertheless, final failure was probably caused by the fall of the patient since the critical failure stress was higher than the minimum ultimate tensile strength, Sut min and close to the typical ultimate tensile strength, Sut typ. In future work, careful attention will be given to the geometric stress raisers characterizing the implant. It will be intent to propose a new implant design more resistant to fatigue without compromising the installation versatility. In addition, an extended study will be necessary to investigate if the bolting procedure can be improved in order to reduce the cyclic load amplitude experienced by the screws and plate. An optimization analysis accounting for the number of screws, their position and their preload are under development. The ideal installation scenario will then be proposed to practitioners to assist surgery.