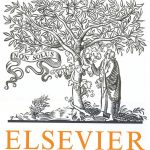
ترجمه مقاله نقش ضروری ارتباطات 6G با چشم انداز صنعت 4.0
- مبلغ: ۸۶,۰۰۰ تومان
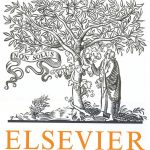
ترجمه مقاله پایداری توسعه شهری، تعدیل ساختار صنعتی و کارایی کاربری زمین
- مبلغ: ۹۱,۰۰۰ تومان
Abstract
A method for modeling the effect of stress relaxation at high temperatures during laser direct energy deposition processes is experimentally validated for Ti-6Al-4V samples subject to different inter-layer dwell times. The predicted mechanical responses are compared to those of Inconel® 625 samples, which experience no allotropic phase transformation, deposited under identical process conditions. The thermal response of workpieces in additive manufacturing is known to be strongly dependent on dwell time. In this work the dwell times used vary from 0 to 40 s. Based on past research on ferretic steels and the additive manufacturing of titanium alloys it is assumed that the effect of transformation strain in Ti-6Al-4V acts to oppose all other strain components, effectively eliminating all residual stress at temperatures above 690 °C. The model predicts that Inconel® 625 exhibits increasing distortion with decreasing dwell times but that Ti-6Al-4V displays the opposite behavior, with distortion dramatically decreasing with lowering dwell time. These predictions are accurate when compared with experimental in situ and post-process measurements.
6 Conclusions
Being able to predict the mechanical response of AM workpieces is important if expensive trial and error iterations are to be avoided. A model has been validated to adequately account for the transformation strain present in Ti-6Al-4V, a common alloy used in direct metal deposition. The model was validated by varying inter-layer dwell times, which are known to impact sample temperature and thus phase transformation effects, for Ti-6Al-4V and Inconel R 625 wall builds. The in situ temperature, in situ distortion, and post-process residual stress predictions were compared with experimental measurements. The Inconel R 625 builds can be adequately modeled without the inclusion of transformation strain, as the alloy does not undergo a solid-state phase transformation. However, for Ti-6Al-4V which does undergo solid-state phase transformation, neglecting the effect of transformation strain incurs errors of over 500% when predicting postprocess residual stress and distortion, and also does not capture the distortion accumulation trends observed during the in situ measurements. Modeling that the transformation strain caused by solidstate phase transformation in Ti-6Al-4V acts to fully relax the residual stress at temperatures above 690◦C, leads to close agreement with experimental measurements. This modeling effort highlights the need for future work focusing on further development of a high-temperature constitutive model for Ti-6Al-4V. High temperature Gleeble testing could provide insight into the dynamic nature of the strain relaxation noted in Ti-6Al-4V. Better understanding of the relationship between temperature, microstructure, and material properties is needed to develop a more physically realistic constitutive model.