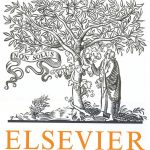
ترجمه مقاله نقش ضروری ارتباطات 6G با چشم انداز صنعت 4.0
- مبلغ: ۸۶,۰۰۰ تومان
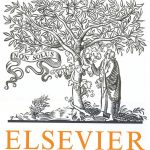
ترجمه مقاله پایداری توسعه شهری، تعدیل ساختار صنعتی و کارایی کاربری زمین
- مبلغ: ۹۱,۰۰۰ تومان
Circular saws have the potential to be part of a high-efficiency machining method for carbon fiberreinforced plastic (CFRP) compared to endmills and abrasive water jet cutting. This paper highlights the characteristics of machined surfaces and tool failure when CFRP was cut by circular saw. A circular saw is a thin, disk-shaped cutting tool; hence, the saw body often exhibits out-of-plane vibration during the machining process. This vibration affects the quality of the machined surface, as well as tool wear. In order to clarify the effect of vibration on machining characteristics, cutting tests were conducted with / without a pair of damping alloy sheets on either side of the circular saw body. Damping alloy sheets can suppress vibration amplitude. Characteristics of machined surface and tool wear were improved by damping. Surface roughness along the feed direction and laminated direction were 0.5 m Ra and 1.1 m Ra, respectively. In addition, we assessed the relationship between carbon fiber orientation and tool wear on CFRP cutting by circular saw. Four fiber orientations (0°, 45°, 90° and -45° against the feed direction) were tested. Cutting force, tool wear, and machined surface were measured after unidirectional CFRP cutting. Results showed that cutting force order was 0°> ±45° > 90°. Furthermore, finished surface quality was also affected by fiber orientation, with a good surface obtained for 0° fiber orientation, and smaller tool side-flank wear with -45°.
6. Conclusions
In this paper, we investigated the particular characteristics of machined surface and tool failure in CFRP cutting by circular saw, and demonstrated the machining capability of the circular saw for CFRP. Our findings can be summarized as follows.
1) In order to improve the low stiffness and damping capacity, a pair of damping alloy sheets was positioned on either side of the circular saw body. The amplitude of frequency at which the cutting edge cut the CFRP was then smaller compared to without damping. Moreover, with damping alloy sheets, side-flank wear and surface roughness were also improved.
2) As feed rate became high, cutting force increased and machined surface quality worsened. Meanwhile, amount of tool wear for the same cutting length decreased, because the frequency of the abrasion becomes lower with the increase of feed rate.
3) Unidirectional CFRP plates with different fiber orientations were machined with a circular saw. Cutting force was largest in the case of 0° fiber orientation, followed by ±45° and 90° cases. This corresponds to the number of cutting fibers. In addition, the finished surface quality was also affected by the fiber orientation; a good surface was obtained in the case of the 0° fiber orientation, and tool side-flank wear was smallest in the case of -45° fiber orientation.