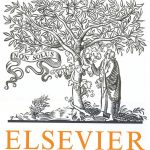
ترجمه مقاله نقش ضروری ارتباطات 6G با چشم انداز صنعت 4.0
- مبلغ: ۸۶,۰۰۰ تومان
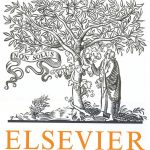
ترجمه مقاله پایداری توسعه شهری، تعدیل ساختار صنعتی و کارایی کاربری زمین
- مبلغ: ۹۱,۰۰۰ تومان
Abstract
NC machining of a nonzero genus triangular mesh surface is being more widely confronted than before in the manufacturing field. At present, due to the complexity of geometry computation related to tool path generation, only one path pattern of iso-planar type is adopted in real machining of such surface. To improve significantly 5-axis machining of the nonzero genus mesh surface, it is necessary to develop a more efficient and robust tool path generation method. In this paper, a new method of generating spiral or contour-parallel tool path is proposed, which is inspired by the cylindrical helix or circle which are a set of parallel lines on the rectangular region obtained by unwrapping the cylinder. According to this idea, the effective data structure and algorithm are first designed to transform a nonzero genus surface into a genus-0 surface such that the conformal map method can be used to build the bidirectional mapping between the genus-0 surface and the rectangular region. In this rectangular region, the issues of spiral or contour-parallel tool path generation fall into the category of simple straight path planning. Accordingly, the formula for calculating the parameter increment for the guide line is derived by the difference scheme on the mesh surface and an accuracy improvement method is proposed based on the edge curve interpolation for determining the cutter contact (CC) point. These guarantee that the generated tool path can meet nicely the machining requirement. To improve further the kinematic and dynamic performance of 5-axis machine tool, a method for optimizing tool orientation is also preliminarily investigated. Finally, the experiments are performed to demonstrate the proposed method and show that it can generate nicely the spiral tool path or contour-parallel tool path on the nonzero genus mesh surface and also can guarantee the smooth change of tool orientation.
8. Conclusion and future works
This paper proposes a novel method of generating tool path for 5-axis machining of the mesh surface with nonzero genus, including the continuous CC tool path and the smooth tool orientation. The proposed tool path method reduces the task of generating the spiral or contour-parallel tool path to the planning of much simple guide line in a rectangle, thus avoiding the complicated geometry computation, such as curve offsetting and self-intersection elimination involved in the traditional methods, etc. The analytical formula of computing CC point and parameter increments for the guide line are first derived on the discrete mesh. This makes the users can control more easily the machining accuracy than before. The real machining experiments are also performed to demonstrate the superiority to other methods. Another point worth mentioning is a simple and efficient method of optimizing tool orientation is also proposed which works directly on the rotary axis coordinate in MCS and can guarantee the motions of rotary axes of 5-axis machine tool as smooth as possible and the improvement on the kinematic and dynamic performance of 5-axis machine tool has been confirmed by the experimental results. Moreover, since the proposed algorithm only involves solving a linear equation system, it is also very efficient, which has been also already demonstrated by our experiments. In our experiments, it is also found that the benefits of our method may decrease with the increase of genus and holes distribution becoming more complicated. Although it can be nicely applicable to the industrial part like mouse, how to further enhance the adaptability of our method still needs more researches to be done in the future works. In addition, the experiment of tool orientation optimization validates the feasibility of the proposed method, but the influences of adjusting tool orientation on the motion of three translational axes, X-, Y- and Z-axis, of machine tool and the federate and how to reposition the tool according to the optimized tool orientation are also worth being further explored.