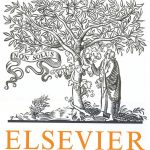
ترجمه مقاله نقش ضروری ارتباطات 6G با چشم انداز صنعت 4.0
- مبلغ: ۸۶,۰۰۰ تومان
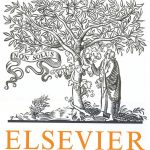
ترجمه مقاله پایداری توسعه شهری، تعدیل ساختار صنعتی و کارایی کاربری زمین
- مبلغ: ۹۱,۰۰۰ تومان
Abstract
In this work, the suitability of using kaolin–styrofoam, sawdust, and high density polyethylene to produce porous ceramic bodies was experimentally investigated. The kaolin samples (raw and beneficiated) were characterized by the XRD, SEM, TGA/DSC and FTIR methods. Batch formulations of the samples including the kaolin and pore formers were formed into green bodies and fired to 1150 °C. The porosities of sintered bodies were calculated and gave the following: apparent porosity: 28.63%–67.13% for all the samples investigated. Samples with high density polyethylene (HDPE) pore formers showed minor surface cracks after firing, but exhibited the highest porosity levels while samples with styrofoam and saw dust exhibited uniform surface characteristics with pores, thermal stability and no visible surface cracks. It can be concluded that formulations containing 80% kaolin can be used for the production of ceramics with porosities as high as 67% if the right pore formers are used.
4. Conclusions
The viability of producing porous ceramic bodies from West African regional kaolin deposits using various pore formers at elevated temperature (≈1150 °C) for catalytic substrate applications has been successfully explored. The XRD analysis of the samples using the Hinckley's index and Scherrer theory indicates that the Kibi kaolin which was used as a plasticizer was well ordered than the Kankara kaolin. This was morphologically confirmed from the scanning electron microscopy data. TG/DSC has been used to study the thermal behaviors of the various samples. From optical and electron microscopy studies, it was observed that after firing at 1150 °C, the as-formed uniform compact green bodies containing combustible pore formers become distorted. Samples with high density polyethylene as pore former resulted in porous bodies, confirming that the choice of pore formers is critical in achieving porous ceramic bodies. Formulations containing 80% kaolin can be used for the production of porous ceramics with porosities as high as 67% employing the appropriate pore formers for specific applications.