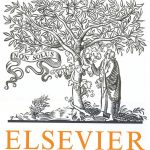
ترجمه مقاله نقش ضروری ارتباطات 6G با چشم انداز صنعت 4.0
- مبلغ: ۸۶,۰۰۰ تومان
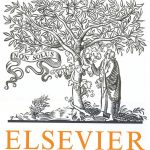
ترجمه مقاله پایداری توسعه شهری، تعدیل ساختار صنعتی و کارایی کاربری زمین
- مبلغ: ۹۱,۰۰۰ تومان
Abstract
This report details a cost-effective new process for transforming mixed waste glass into highvalue building materials without remelting. Worldwide, waste glass is a growing burden and new options are urgently needed for the large volumes of speciality, mixed, broken and contaminated glass that cannot currently be recycled. Conventional glass recycling technologies are limited by the need to separate waste glass into different glass types and the extreme sensitivity of the remelting process to any contamination. In this study, we demonstrated that mixed broken glass could be used as primary input in the production of polymeric glass composites. The composites’ mechanical properties, utility, aesthetic appeal and expected market value were comparable to natural and engineered stone products, widely used as kitchen and bathroom benchtops and floor and wall tiles. Waste glass powder with an average particle size smaller than 108µm was ground then mixed with resin as a binder before the mixture was hot-pressed under pressure. Various ratios of waste glass to resin binder, as well as the effect of a coupling agent and reinforcing mesh were tested. The optimum PGC achieved a flexural strength of 48 MPa, water absorption below 0.002%, a density of 2.113 kg/m3 and compressive strength of 101 MPa with minimum scratch, wear and UV degradation behaviour. Its excellence in the mechanical value stand in parallel with engineering stone but, with cheaper and efficient process. Additionally, this new recycling process embodies an important unique alternative to the remelting of waste glass with the potential to deliver economic and environmental benefits wherever waste glass is stockpiled.
4. Conclusion
This study demonstrates the successful manufacture of high-performance artificial construction slabs from waste glass powder filler. With high compression pressure, heat and an optimal mixing ratio, a densified polymeric glass composite (PGC) panel with a flexural strength of 26 MPa, a compressive strength of 101 MPa and water absorption below 0.0032% was produced. The flexural and compressive strength of the PGCs was found to improve 1significantly to 47.8 and 122 MPa, respectively, with the addition of a 2% coupling agent. The increases were due to the improved adhesion between the resin and glass powder. However, further additions, from 3-5%, showed the reverse effect. As more coupling agent was used, the surface glass powder became enwrapped by -OH again, leading to poor compatibility and weak interface bonding with the resin, leading to a deterioration in the mechanical properties of the composite. Further investigation also showed the addition of a coupling agent from 0-5% showed negligible improvement in both water absorption and hardness. As an alternative to a coupling agent, a sheet of fibreglass was successfully tested as a cheaper means of improving the flexural strength of the PGCs, particularly for thin, narrow slabs. Wear, scratch, thermal decomposition and fire retardancy of PGC were also investigated and are found to be comparable with engineering stone. To improve the aesthetic appeal, other waste such as coloured stone, copper powder from e-waste and tinted broken glass can also be added. These results demonstrated that a high quality and versatile product, comparable to engineered stone, could be produced primarily from waste glass powder. Given the emerging global challenged posed by waste and the need for low-cost, locally available inputs for manufacturing, this process offers an important alternative for the waste glass that cannot be remelted in conventional recycling processes. As such, it has the potential to deliver significant economic and environmental benefits to almost any community, given the relatively simple manufacturing process and the wide availability of waste glass.