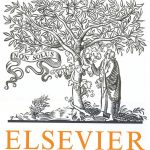
ترجمه مقاله نقش ضروری ارتباطات 6G با چشم انداز صنعت 4.0
- مبلغ: ۸۶,۰۰۰ تومان
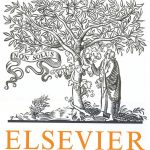
ترجمه مقاله پایداری توسعه شهری، تعدیل ساختار صنعتی و کارایی کاربری زمین
- مبلغ: ۹۱,۰۰۰ تومان
abstract
A computational fluid dynamics (CFD) model representing the effect of wafters in a totally enclosed electric machine is presented, introducing the most relevant theoretical assumptions and simplifications. The validation of the model is conducted through experimental measurements. From the CFD simulation data, a second-order response surface is developed using statistical tools, from which the wafters’ influence on the convective heat transfer from the stator end windings is predicted. Wafter design criteria are obtained from the response surface information. Finally, a specific case is analysed, showing through CFD simulations that temperatures in the machine are reduced by including wafters in the design.
Conclusions
The effect of including wafters in a totally enclosed machine with wound windings was analysed using statistical tools and CFD simulations, and the following conclusions were obtained:
The inclusion of wafters in a specific machine is translated into a considerable reduction in temperatures and an increase in ventilation losses, which is essential for thermally required designs. For the example given, a reduction of 16.2 C was obtained.
Wafter design can be approached using statistical tools such as DoE, where the optimum configuration can be obtained for a limited region. Based on the statistical model obtained, for the particular case of a totally enclosed machine with wound windings, design criteria for minimizing temperatures is obtained.
Second-order statistical models can accurately determine the convective heat transfer coefficient for a wide range of topologies, which can be very beneficial for modelling analytical thermal models.
The effect of the number of wafters on the convective heat transfer was not analysed in detail, so a deeper analysis should be performed in order to get better insight into the influence of this parameter.
Although this paper focuses on wound windings, the methodology could be applied to any kind of windings, such as coil-form windings or hairpin windings, in future research.