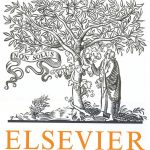
ترجمه مقاله نقش ضروری ارتباطات 6G با چشم انداز صنعت 4.0
- مبلغ: ۸۶,۰۰۰ تومان
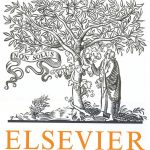
ترجمه مقاله پایداری توسعه شهری، تعدیل ساختار صنعتی و کارایی کاربری زمین
- مبلغ: ۹۱,۰۰۰ تومان
abstract
In this study, continuous lignin fibers from switchgrass have been successfully synthesized via multifilament melt-spinning and converted to carbon fibers using optimized stabilization and carbonization techniques. Unidirectional lignin carbon fiber reinforced composites are produced using a vacuum assisted resin transfer molding process for the first time. Produced lignin carbon fiber is evaluated in mechanical, interfacial, and microstructural areas. Single fiber mechanical properties are characterized using a unique MTS Bionix Nano-UTM. Interfacial properties and resin/fiber behavior are evaluated using single fiber fragmentation. Microstructural properties are determined using wide-angle x-ray diffraction. Mechanical results indicated an initial tensile modulus along fiber axis of 36 GPa and a failure stress of 600 MPa for single carbon fibers. Lignin carbon fibers demonstrate a nonlinear increase in modulus with applied tensile strain similar to recently observed for commercial poly-acrylonitrile (PAN) carbon fibers. Microscopy revealed few defects within and along the lignin carbon fibers, and the processed lignin fibers demonstrated minimal crystalline regions and crystallite alignment when compared to commercial PAN based fibers. Interfacial shear strength with epoxy resin was found to be 17 MPa with a fiber fracture length of 228 μm. Unidirectional composite coupons achieved tensile modulus of 9 GPa and a failure strength of 85 MPa at 1% failure strain. Lignin carbon fiber and composites produced are targeted for non-structural applications as mechanical properties are currently less than PAN carbon fibers and therefore are not suitable to replace PAN carbon fiber at this stage. Relatively low composite strength is the likely result of fiber layup, fiber fusing, and non-continuous fibers across the gage length of the composite. Nano-tensile and interface shear strength results presented here have important implications for lignin carbon fiber composite development to optimize fiber/resin bonding. In addition, composite manufacturing procedures detailed here are a major step forward in the development of sustainable carbon fiber composite production.
4. Conclusion
Organosolv fractionated lignin carbon fiber was produced and characterized via Nano-UTM, Single Fiber Fragmentation, and XRay Diffraction. In addition, a unidirectional carbon fiber reinforced polymer composite was manufactured with the lignin carbon fiber through a modified VARTM process. Lignin carbon fiber exhibited little to no surface defects from SEM and optical microscopy. Mechanical results for the carbon fiber indicated an average modulus close to 36 GPa and failure stress of ~600 MPa (3.66 and 630 MPa shape and scale parameters). Interfacial shear strength values were relatively high around ~16 MPa for unsized lignin carbon fiber. SFFT saturated samples revealed fiber fractures propagating into the matrix and no fiber pullout. These interface strength results indicate that lignin carbon fiber would be ideal for applications that take advantage of interfacial strengths such as chopped fiber composites or fillers. XRD results and analysis demonstrated little to no crystalline regions in the fibers, which is likely the reason for low modulus of the fibers compared to commercially available PAN based fibers. Nevertheless, lignin based carbon fibers tend to follow the same strain hardening trend found in other carbon fibers, which may indicate a general rearrangement of amorphous carbon when strain is applied. After the lignin carbon fiber was fully characterized, unidirectional mats were placed in a preform inside a VARTM system and produced into a composite. Fiber alignment and quantity varied across the panel during production. The composite panel mechanical properties were ~9 GPa and ~85 MPa for modulus and failure strength, respectively. Composite samples demonstrated lateral brittle failures in the gage region indicating a large ratio of interface to mechanical strength. Produced lignin carbon fiber composites exhibited non-explosive failure mechanisms with minimal fiber pullout as seen in SFFT. Overall, the lignin carbon fiber demonstrated acceptable mechanical and interfacial properties for potential applications in chopped carbon fiber composites for structural applications. This advantage of lignin based carbon fiber over commercial PAN based carbon fibers (that require additional sizing) suggests that lignin carbon fiber would be preferable in some applications that mobilize the interface such as discontinuous fiber based composites, fused deposition modeling for additive manufacturing, and fillers. Results presented in this study are a significant improvement to current lignin carbon fiber characterization techniques and lignin carbon fiber composite manufacturing. Continued development and improvement of the mechanical performance will open more utilization of lignin carbon fiber, particularly in automotive applications.