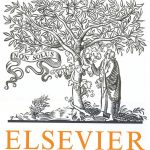
ترجمه مقاله نقش ضروری ارتباطات 6G با چشم انداز صنعت 4.0
- مبلغ: ۸۶,۰۰۰ تومان
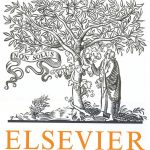
ترجمه مقاله پایداری توسعه شهری، تعدیل ساختار صنعتی و کارایی کاربری زمین
- مبلغ: ۹۱,۰۰۰ تومان
Abstract
Current rotary blade choppers for sugarcane harvesting have the disadvantage of becoming clogged with leaves/cane around the rotating blades causing them to hit the ground and rocks that result in rapid blade wear and tear. Dull blades require repeated cane cutting attempts causing damage to the cane and increasing the cutting force and energy requirements. Thus, the search for alternative, non-contact, cutting options such as waterjet (WJ) cutting has been undertaken. The results indicated that WJ cutting has potential but weaknesses have also been reported. Hence, this study explored the use of abrasive fine sand (AWJ) to overcome the weaknesses of the pure WJ cutting application. Using the Hoogstrate model and a MATLAB program, AWJ cutting simulation was performed using an orifice and nozzle diameter combination of 0.25 and 0.76 mm at 360 MPa water pressure, respectively, which produced a water flow rate of 1.6 L/min and a power input of 15 kW. Other parameters used in the test included: 80 mesh fine river sand abrasive materials, a specific cutting energy of 8.7 × 10−3 J/mm3 and a fitted cutting efficiency of 0.35. The experimental results revealed that the system was able to cut sugarcane stalks completely at a much farther standoff distance by reducing the traverse speed. The study also showed that cutting sugarcane of 30 and 120 mm diameters would require a traverse speed of 4.4 km/h and 1.1 km/h, respectively. The results implied that limitations should be set for sugarcane thickness for the optimum traverse speed and a standoff distance should be set to no more than 210 mm with a minimum traverse speed of 0.6 km/h.
Conclusion
Abrasive waterjet cutting simulation for sugarcane cutting was performed by investigating the relationship between WJ and AWJ cutting parameters. Using an AWJ with an orifice diameter of 0.25 mm and water pressure 360 MPa, Valco WJ's cutting performance was improved by reducing the actual water flow rate and the power input down by 50% and 58.8%, respectively. The specific cutting energy selected was at 8.7 103 J/mm3 with an equivalent cutting efficiency of 0.35. Selection was based on the fitted stainless steel (INOX) cutting data of Lefevre et al. (2004). The traverse speed obtained using the Hoogstrate model for cutting aluminum and stainless steel with the respective cutting effi- ciencies of 0.17 and 0.15 were comparable to the introduced traverse speed given by the KMT Waterjet (2015). The aluminum and stainless steel cutting simulations obtained from the model's calculated traverse speeds were within the range of the introduced traverse speeds of the KMT waterjet, showing that the Hoogstrate model can reliably be used to predict cutting parameters for ductile materials. The results of the sugarcane cutting experiment have shown that an AWJ has a greater cutting capability than a WJ. Substituting garnet abrasive materials with fine river sand was also proven to be feasible based on the 5 mm steel plate cutting test results. The test further showed that an AWJ was capable of cutting sugarcane stalks even at an increased standoff distance of 250 mm by reducing the AWJ traverse speed.