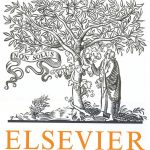
ترجمه مقاله نقش ضروری ارتباطات 6G با چشم انداز صنعت 4.0
- مبلغ: ۸۶,۰۰۰ تومان
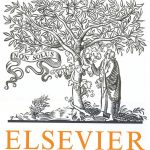
ترجمه مقاله پایداری توسعه شهری، تعدیل ساختار صنعتی و کارایی کاربری زمین
- مبلغ: ۹۱,۰۰۰ تومان
It is often observed that the plastic deformation of crystalline polymers, especially on drawing, causes significant amount of cavitation. Cavitation can be suppressed in the process of rolling due to compressive component. An innovative method of obtaining highly oriented polymeric materials is by unidirectional rolling in a channel formed on the circumference of one roll with another roll, having the thickness matching the width of the channel. The side-walls of the channel on one roll constitute the side constraints while the other roll works like a plunger in channel-die. Rolling with side constraints is cavity-free and is advantageous over conventional rolling, channel-die compression or solid state extrusion since it gives the possibility of obtaining relatively thick and infinitely long highly-oriented shapes or profiles in a fast continuous manner. The resulting profiles can have considerably high cross-section area. The design of the rolling machine is described. Few examples of rolling with the rate 4.23 m min−1 of isotactic polypropylene (iPP) and high density polyethylene (HDPE) shapes are presented. Tensile strength of the rods rolled to the compression ratio 5.4–6.6 with final cross-section of 10–12 mm approached 200 MPa for both polymers. The oriented rods of iPP and HDPE demonstrated high and sharp texture produced in HDPE by the activity of (100) [001], (010) [001] and (100) [010] crystallographic slips while in iPP (010) [001], (110) [001] and (100) [001] slip systems were active. In addition to those slips twinning modes were active on unloading. Appropriate combination of rolling rate, temperature, initial thickness of rolled bar, as well as molecular weight of the polymer will apparently lead to rods with higher strength.