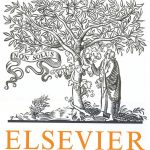
ترجمه مقاله نقش ضروری ارتباطات 6G با چشم انداز صنعت 4.0
- مبلغ: ۸۶,۰۰۰ تومان
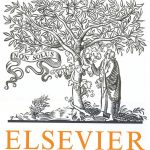
ترجمه مقاله پایداری توسعه شهری، تعدیل ساختار صنعتی و کارایی کاربری زمین
- مبلغ: ۹۱,۰۰۰ تومان
Abstract
Highly accurate model predictions contribute to the performance and stability of model predictive control. However, high fidelity models are difficult to implement in real time control due to the large and often nonconvex optimization problem that must be completed within the feedback cycle time. To address this issue, a switched control scheme that uses high fidelity model predictions in real time control is presented. It uses real time simulated data to identify a linear empirical control model. The real time model identification procedure does not interrupt the process, and is suitable for nonlinear processes where offline model identification is difficult. Controller stability is discussed, and the control scheme is demonstrated in a managed pressure drilling simulation. The switched controller provides improved performance over both a high fidelity model based controller and a nonadaptive empirical model.
5. Conclusion
A switched control scheme is presented that makes use of a high fidelity model running in parallel with a process. The high fidelity model is used to generate simulated data to identify the model parameters of a linear empirical control model in MPC. During the model identification procedure, the switch implements a low order control model to control the process. In this way the model identification procedure does not disrupt the controller. The model identification procedure is triggered when the error in the past predictions of a linear model exceeds a prescribed threshold. The switched control scheme allows the highly accurate predictions of a high fidelity model to be incorporated in real time control without the high online computational cost. The control scheme is applied to a simulated managed pressure drilling process. The controller performance is demonstrated under set point tracking and disturbance rejection scenarios. Future work on the control scheme includes updating the high fidelity model parameters with process data with moving horizon estimation, and controlling a process when feedback is lost and highly accurate model predictions are necessary.