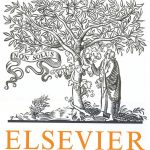
ترجمه مقاله نقش ضروری ارتباطات 6G با چشم انداز صنعت 4.0
- مبلغ: ۸۶,۰۰۰ تومان
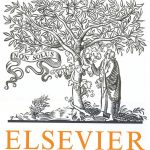
ترجمه مقاله پایداری توسعه شهری، تعدیل ساختار صنعتی و کارایی کاربری زمین
- مبلغ: ۹۱,۰۰۰ تومان
Abstract
Recent advances in 3D printing technologies bring wide range of applications from fast prototyping to product manufacturing. However, one intrinsic limitation of 3D printing is that we cannot fabricate a single object that is larger than the working volume of a 3D printer. To address this issue, we may partition the given object into 3D parts of manageable sizes for printing, and then assemble the object from the printed 3D parts. Rather than using connectors, glue, or skew, we propose to connect the printed 3D parts by 3D interlocking such that the assembled object can be not only repeatedly disassembled and reassembled, but also strongly connected by the parts' own geometry. To achieve these, we develop a voxelization-based approach to partition a given 3D model into 3D interlocking parts. To guarantee the generated 3D parts to be structurally sound and well-connected by 3D interlocking, we deform the local geometry of the 3D model to avoid voxel fragmentation, employ internal voxels to create initial interlocking parts, and analyze the local shape within voxels to guide the final parts construction. We demonstrate the effectiveness of our approach on 3D models with a variety of shapes, and realize some of them by 3D printing.
7. Conclusion
This paper presents a novel voxelization-based method to partition a given 3D object model of general shape into interlocking 3D parts such that the 3D object can be printed with smaller parts that are connected by 3D interlocking. We first voxelize the input 3D model and analyze the local shape within each voxel, where a local deformation strategy is developed to avoid voxel fragmentation in the voxelization. Second, we differentiate internal and boundary voxels according to the local shape contained and employ internal voxels to create initial 3D interlocking parts. Lastly, we apply the local shape information encoded by shape and saliency connection graphs to guide the construction of final parts’ geometry. By these, we can generate 3D parts that are structurally sound and strongly connected by 3D interlocking, without obvious cutting seams across salient object features. We validate the performance of our method by fabricating a variety of models using different types of 3D printers, and also demonstrate its feasibility by designing and making the 22-parts interlocking ring.