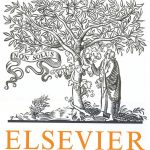
ترجمه مقاله نقش ضروری ارتباطات 6G با چشم انداز صنعت 4.0
- مبلغ: ۸۶,۰۰۰ تومان
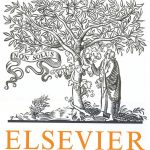
ترجمه مقاله پایداری توسعه شهری، تعدیل ساختار صنعتی و کارایی کاربری زمین
- مبلغ: ۹۱,۰۰۰ تومان
ABSTRACT
Multi-objective layout optimization methods for the conceptual design of robot cellular manufacturing systems are proposed in this paper. Robot cellular manufacturing systems utilize one or more flexible robots which can carry out a large number of operations, and can conduct flexible assemble processes. The layout design stage of such manufacturing systems is especially important since fundamental performances of the manufacturing system under consideration are determined at this stage. Layout area, operation time and manipulability of robot are the three important criteria when it comes to designing manufacturing system. The use of nature inspired algorithms are not extensively explored to optimize robot workcell layouts. The contribution in this paper is the use of five nature-inspired algorithms, viz. genetic algorithm (GA), differential evolution (DE), artificial bee colony (ABC), charge search system (CSS) and particle swarm optimization (PSO) algorithms and to optimize the three design criteria simultaneously. Non-dominated sorting genetic algorithm-II is used to handle multiple objectives and to obtain pareto solutions for the problems considered. The performance of sequence pair and B*-Tree layout representation schemes are also evaluated. It is found that sequence pair scheme performs better than B*-Tree representation and it is used in the algorithms. Numerical examples are provided to illustrate the effectiveness and usefulness of the proposed methods. It is observed that PSO performs better over the other algorithms in terms of solution quality.
7. Conclusion
Genetic algorithm, differential evolution, particle swarm optimization, artificial bee colony and charged system search algorithms are proposed to solve robot workcell layout problems. The performance of these five algorithms are evaluated using ten problems generated randomly. Three objective functions are considered in this paper, viz, Layout area, operation time and manipulability of robot. The implementation details of all the algorithms are presented. Two layout representation schemes, B*tree and sequence pair are evaluated and found that sequence pair representation scheme performs better. The parameters of the five nature inspired algorithms considered in this paper are fine-tuned to get better results. The assembly robot used to illustrate the problem is Mitsubishi RV-6SQ. Two objective case and three case of the problems are analysed separately and the results are presented. NSGA-II is used to handle multiple objectives and to optimize them simultaneously. It is found that PSO performs better over other algorithms. Bestlayouts for the two-objective three-objective cases are generated using PSO. The best layout design was found by optimizing three objectives simultaneously as there is trade-off among the objective functions. Future research work could expand the cell size with more number of machines and more number of robots. Another research direction could be to develop layout representation schemes, which are efficient and fast to generate layouts.