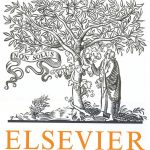
ترجمه مقاله نقش ضروری ارتباطات 6G با چشم انداز صنعت 4.0
- مبلغ: ۸۶,۰۰۰ تومان
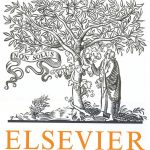
ترجمه مقاله پایداری توسعه شهری، تعدیل ساختار صنعتی و کارایی کاربری زمین
- مبلغ: ۹۱,۰۰۰ تومان
Abstract
Recently Cu-Al-Ni shape memory alloys have gained special attention due to their high temperature applications. This article attempts to formulate the various processing routes for processing of Cu-Al-Ni shape memory alloys such as casting route, powder metallurgy route, rapid solidification and spray forming process. The pros and cons of various processes are provided in detail. The additive manufacturing, which is an emerging process is discussed which could be a promising technique of preparing CuAl-Ni shape memory alloys. Further recommendations are provided in terms of producing fine-grained near net shaped shape memory alloys for high temperature applications.
Summary
Table 1 summarizes the State of the art for the preparation of Cu-Al-Ni Shape memory alloy. The conventional casting method for preparing Cu-Al-Ni shape memory alloy suffers from a disadvantage that it produces coarse grain structure of the order of ~ 1 mm and is prone to brittle fracture [51]. Therefore, the brittleness is a severe problem in cast Cu-Al-Ni alloys due to large grain size combined with large elastic anisotropy. Several efforts are made in developing fine grained Cu-Al-Ni shape memory alloys with improved mechanical properties. Casting using addition of quaternary element such as Ti, Zr, V and B have shown a significant grain refinement and improvement in the mechanical properties of the Cu-Al-Ni shape memory alloy. When a second phase is present in the matrix phase, the grain growth is hindered because of the grain boundary pinning caused due to the interaction of the grain boundary with the particle. However, compositional control during casting and limitations to achieve the desired level of grain size restricted further development of the alloy. Moreover, hot working of the cast Cu-AlNi alloy are attempted to reduce the grain size, which would temporarily reduce the grain size, however recrystallization and grain growth during a properly controlled homogenization stage reduces the final mechanical property of the alloy. Therefore, there is a need to retain the high temperature deformation structure by retarding the effect of recrystallization by immediately quenching the hot rolled samples after the final rolling pass. This would result in the formation of fully martensitic structure which reduces the grain growth coupled with increased mechanical property of alloys.