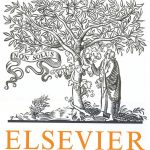
ترجمه مقاله نقش ضروری ارتباطات 6G با چشم انداز صنعت 4.0
- مبلغ: ۸۶,۰۰۰ تومان
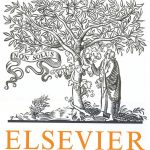
ترجمه مقاله پایداری توسعه شهری، تعدیل ساختار صنعتی و کارایی کاربری زمین
- مبلغ: ۹۱,۰۰۰ تومان
Abstract
Cu-based shape memory alloys are potential substitutes of NiTi shape memory alloys, owing to their lower production costs and recent increase in their mechanical properties arising from better control of the microstructure. The development of joining technologies for advanced materials is key to expand to the potential applications of any engineering alloy. In this work, laser welding of single crystal-like Cu-Al-Be shape memory alloys was performed. The microstructure and tensile properties were evaluated to understand the effect of laser welding on the microstructural and mechanical features of the welded joints. Cycling tests performed for a wide range of temperatures revealed that the joints possess extraordinary superelastic recovery after joined, with potential applications in damping devices due to the significant amount of energy that can be absorbed during superelastic deformation.
4. Conclusions
Defect-free joints were obtained when laser welding of Cu-Al-Be shape memory alloys and this study shows the potential to use such high energy density welding process for joining these alloys. The following major conclusions can be drawn:
- The crystallographic texture of the fusion zone was not modified by the welding processes, following the same orientation as the base material;
- No significant hardness changes were determined between the fusion zone and base material;
- The tensile strength of the laser welded joints is slightly lower than the base material (686 vs 631 MPa), whereas the tensile strain was higher for the welds (50.8 vs 54.1 %). This was attributed to the microstructure in the fusion zone, which sustain a higher amount of deformation owing to the presence of obstacles that oppose to crack propagation.
- Superelastic behaviour of the welded joints was preserved with associated high energy absorption capabilities and transformation strain. Moreover, at both -40 and 100 ⁰C, the laser welded joint exhibit superelastic behaviour. These features make these joints potential candidates for applications requiring large damping capabilities, such as in seismic systems.