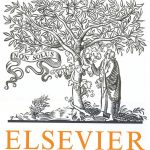
ترجمه مقاله نقش ضروری ارتباطات 6G با چشم انداز صنعت 4.0
- مبلغ: ۸۶,۰۰۰ تومان
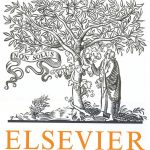
ترجمه مقاله پایداری توسعه شهری، تعدیل ساختار صنعتی و کارایی کاربری زمین
- مبلغ: ۹۱,۰۰۰ تومان
Abstract
The failure of shell and tube heat exchangers caused by solid particle erosion has been a major problem in the oil and gas and other industries. Predicting erosion is still a developing art, an accurate simulation method is then significant to analyze the erosion characteristics in such complex geometry and determine erosion rate of metal surface. In this work a physical model was proposed to simulate the erosion of two-pass shell and tube heat exchangers with computational fluid dynamics. The simulation was performed for different feed fluid rates and a range of sand particle sizes from 0.1 to 1000 μm. The erosion rates of tube sheet, tube ends in the inlet plenum and the inner wall of tubes were monitored and the influences of flow pattern, particle size and particle behaviors on erosion were studied. The predictions are compared with the earlier studies and a good agreement was found. The particles can be classified into three groups based on the dependence of erosion rates of tube sheet and tubes on the particle size. The large particles (>200 μm) exhibited a near-linear influence on the erosion rates. The small particles (about 50–200 μm) produced approximate size-independence facet-average erosion rate of tubes, but the maximum local erosion rates of the tubes and tube sheet sharply increased with the decrease of particle size. The fine particles (<about 50 μm) resulted in low facet-average erosion rates but very high local erosion rate. The erosion at the tube sheet, tube end and tube surface also show different aspects of relation with particle size.
4. Conclusions
The erosion of a two-pass shell and tube heat exchanger was simulated by modelling the flow and particle motion with a physical model, where each individual tube was presented by a short tube plus a porous plug and a porous plate was used to adjust the backpressure in the rear head. This approach revealed more flow aspects affecting the erosion of the head and tubes of the heat exchanger, compared to the treating not including the modelling of flow in the rear head and the second pass. The model includes both the flow field in the development section of each tube and the deviation of flow rates through the tubes into the affecting parameters on erosion. The fluid flow was described with RANS and SST-k-ω turbulence models, while the sand particles in the shell and tube heat exchanger were investigated using the Lagrangian particle tracking method. The erosion was predicted for sand particles of 0.1 to 1000 m in diameter. It was found that the erosion caused by large particles was inconsistent with the flow pattern due to the separation of the particles having high inertia from the flow stream, when the flow direction changes, while the erosion due to small particles of less than 100 m can be represented by the flow characteristics, such as the flow direction and velocity magnitude.