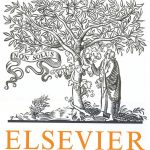
ترجمه مقاله نقش ضروری ارتباطات 6G با چشم انداز صنعت 4.0
- مبلغ: ۸۶,۰۰۰ تومان
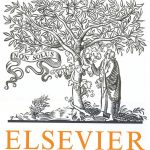
ترجمه مقاله پایداری توسعه شهری، تعدیل ساختار صنعتی و کارایی کاربری زمین
- مبلغ: ۹۱,۰۰۰ تومان
Abstract
This study demonstrates that 3D printing technology offers a simple, easy, and cost-effective method to fabricate artificial flaws simulating real cracks from the viewpoint of eddy current testing. The method does not attempt to produce a flaw whose morphology mirrors that of a real crack but instead produces a relatively simple artificial flaw. The parameters of this flaw that have dominant effects on eddy current signals can be quantitatively controlled. Three artificial flaws in type 316L austenitic stainless steel plates were fabricated using a powderbed-based laser metal additive manufacturing machine. The three artificial flaws were designed to have the same length, depth, and opening but different branching and electrical contacts between flaw surfaces. The flaws were measured by eddy current testing using an absolute type pancake probe. The signals due to the three flaws clearly differed from each other although the flaws had the same length and depth. These results were supported by subsequent destructive tests and finite element analyses.
4. Conclusion
This study has proposed the fabrication of artificial flaws simulating that simulate real cracks from the viewpoint of ECT using 3D printing technology. Three artificial flaws in type 316L austenitic stainless steel plates were fabricated to demonstrate that it is possible to quantitatively control not only the length and depth of a flaw, but also its branching and electrical resistance, all which significantly affect its eddy current signals. The validity of the proposed approach was confirmed by eddy current examination, visual examination, and finite element analysis. The densities of the samples fabricated in this study were 7.7 g/cm3, which is approximately 96% of the density of general 316L austenitic stainless steel. No obvious attractive force was confirmed between the samples and permanent magnets, which supports to regard the samples as nonmagnetic. These, as well as the good agreement between the experiment and the simulations, indicate that it is reasonable to regard the samples are basically identical to general type 316L austenitic steel. It should be noted that all information concerning flaw fabrication is recorded in an STL file that can be prepared using CAD software, and no special techniques are necessary. This enables very accurately controllable cracks to be fabricated with high reproductivity. It should be also noted that the machine and raw materials used in this study were generic; no special fabrication instruments were necessary. Although sample fabrication for the present study required over 10 hours, recent developments in 3D printing technology suggest that, in the future, it will be possible to fabricate artificial flaws simulating real cracks with greatly reduced time and cost. It will also be possible to fabricate artificial flaws for other nondestructive testing methods, such as ultrasonic tests, that are more sensitive to microscopic flaw structure.