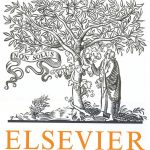
ترجمه مقاله نقش ضروری ارتباطات 6G با چشم انداز صنعت 4.0
- مبلغ: ۸۶,۰۰۰ تومان
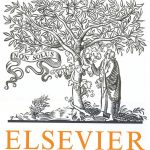
ترجمه مقاله پایداری توسعه شهری، تعدیل ساختار صنعتی و کارایی کاربری زمین
- مبلغ: ۹۱,۰۰۰ تومان
Freeze-drying as an industrial process dates from the time during World War II when the demand for human blood plasma reached critical proportions. Before that, drying by freezing and sublimation of ice had been a laboratory curiosity, although the concentration effects of freezing had been well appreciated very much earlier. Thus, the Uighurs of Turfan prepared ‘frozen-out wine’ as early as the seventh century. Even in present times, however, it is not universally appreciated that freezing is actually synonymous with drying, because solvent water is removed from a solution or a dispersion in the form of a pure solid (ice) phase. The fact that the ice is subsequently sublimed, to be recondensed elsewhere, does not affect the residual solution phase. There are other misconceptions about freezing and drying, among them the notion that ‘…the transformation of water into ice brings to an end all chemical reactions’ [1]. Industrial conventional wisdom also still has it that freeze-drying processes can only be developed empirically by trial and error, i.e. by testing the finished product, or that ‘…anything can be freeze-dried in 24 hours’. It is the purpose of this review to convince the reader that the various stages of lyophilisation are based on very sound physical, chemical and engineering principles and can be controlled to the extent that the outcome of a given process performed on a given product can often be estimated to within fairly close tolerances, without the need for trial-and-error experimentation. Even more important, stable products can frequently be designed by matching an optimum product formulation with its associated optimum drying process cycle.