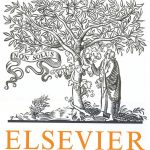
ترجمه مقاله نقش ضروری ارتباطات 6G با چشم انداز صنعت 4.0
- مبلغ: ۸۶,۰۰۰ تومان
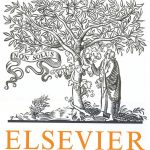
ترجمه مقاله پایداری توسعه شهری، تعدیل ساختار صنعتی و کارایی کاربری زمین
- مبلغ: ۹۱,۰۰۰ تومان
Abstract
In this work an approach to predict the strength of notched structures made of quasi unidirectional glass fibre epoxy is presented. It takes into account the fabric specific behaviour in terms of hardening and softening. Four macroscopic ply failure modes are considered according to the Hashin criterion, depending on the direction of loading. Material hardening and softening is implemented according to Continuum Damage Mechanics. The hardening mechanism is modelled separately for matrix tension and shear. The softening mechanism is modelled by the incorporation of fracture toughness according to the failure mode (fibre/matrix failure in tension/compression). A new technique is proposed to determine the fracture toughness from uniaxial tension/compression tests of unidirectional notched laminate specimens. Special interest is given to the temperature impact on the material properties (elastic parameters, strengths and fracture energy) in a wide range (−40 °C to 160 °C). Since the interval covers the rubber temperature of epoxy the approach’s reliability under such conditions is examined as well.
6. Conclusion
This work shows, that implementing a simple CDM model into FEM simulation not only permits the realistic calculation of notched laminate strengths, but also to simulate more complex structures reasonably. The behaviour of quasi UD GF-EP is examined experimentally. In longitudinal tension, compression and transverse compression linear elastic behaviour is observed. The material behaviour in transverse tension and shear loading is nonlinear. In both cases a yield point is followed by hardening which can be regarded as linear. The material is characterised in a wide temperature range and in dependence of the global FVF. Tests on notched laminates show that the quasi UD GF-EP is rather notch insensitive, in some cases the true specimen strength even exceeded those of unnotched laminates, which is referred to as notch paradoxon. The strength prediction of open hole UD and MD laminates by means of the FEM is examined comprehensively. The key findings of this work are presented in the following: (1) The comparison of simulations and experiments clearly shows that complete a stiffness reduction after element failure, indicated by a modified Hashin criterion, underestimates the specimen strength. Incorporating hardening can lift the calculated strength moderately; still it remains below the measured strength. To calculate realistic values it is mandatory to include the material failure process by CDM into FEM simulations. Additional incorporation of hardening alters the stress strain curve in cases where hardening is observable on specimen level. The Adjustment of the specimen strength is moderate. Fracture toughness turns out to be the decisive parameter in terms of notched laminate strength simulation. (2) A new approach is presented to determine the fracture toughness values for the four failure modes fibre/matrix tension/compression. Laborious fracture toughness tests are avoided. Instead ordinary tension/compression tests on notched UD laminates are used in combination with a multi-target analysis to calibrate the fracture toughness values. The values determined in this manner are used in the simulation of MD laminates. The calculated specimen strengths reasonably agree with experiments, which indicates that the calibration approach is capable of determining useful fracture toughness values. This is emphasised by the simulation of an E-Machine rotor structure. (3) The fracture toughness values derived from RT tests are also applied to simulate longitudinal loading of notched laminates at the epoxy’s rubber temperature (160 C). The stress strain curves agree well. Thus it follows that the fracture toughness in this case is not determined by the temperature sensitive matrix but rather by the fibres. The presented method to calibrate fracture toughness values and their insensitivity to high temperatures contribute to use the benefits of quasi UD GF-EP fabric (cost efficiency and notch insensitivity) and FRP in general in structural application.