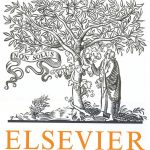
ترجمه مقاله نقش ضروری ارتباطات 6G با چشم انداز صنعت 4.0
- مبلغ: ۸۶,۰۰۰ تومان
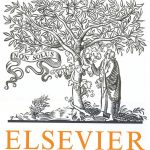
ترجمه مقاله پایداری توسعه شهری، تعدیل ساختار صنعتی و کارایی کاربری زمین
- مبلغ: ۹۱,۰۰۰ تومان
Abstract
Generally, wood chipping represents an important procedure in the wood processing and forestry industry. To improve structural components like chipping tools, knowledge of the properties of local timber including resistance against chipping as well as the dynamically acting process forces is of utmost significance. The aim of this work is to experimentally evaluate service-induced stresses on machinery parts to create a numerical material model, which is capable of revealing similar resistance against cutting as natural wood. To this end, a small-scale cutting machine has been designed, incorporating a bladeholder with strain gauges applied, measuring the resulting mechanical stresses during the chipping process by focussing on different wood species. Spruce is utilized as a variety with a lower density and European beech for higher density timber applications. The test results demonstrate a distinct difference by cutting both materials, whereby European beech indicates more than twice the resistance against chipping compared to spruce. Setting two different, relatively acute rake angles on the cutting tool does not reveal a fundamental difference for chipping. To evaluate the numerical wood material model, an isotropic ductile damage model, usually applied to ductile metals, was implemented in this study. Based on a sensitivity study of the material properties in the course of the numerical simulation, a possible approach is presented that explains how to change the cutting resistance, depending on the blade movement direction and the angle of the main grain of the timber. In a comparison of different types of mechanical stress from the numerical analysis and experimental tests, the results exhibit strong correlation. Element damage and deletion correspond at similar load levels, exhibiting a deviation of no more than 24%.
Conclusion
This work illustrates a possibility to numerically calculate service-induced stresses on machinery parts occurring by means of the dynamic process of chipping wood. Therefore, a concept of a customized damage model is applied. It incorporates the wooden anisotropic behaviour for cuts with a variation of isotropic material parameters in dependence of the cutting and the wood grain direction. Herein, established material characteristics in different cutting directions are employed and a study on process-relevant variables has been performed to achieve a similar resistance against cutting to that provided in the test results. Experimental smallscale cutting tests were conducted to measure the cutting resistance of a relatively dry spruce specimen and European beech. The tests measured the marked dependence of the chipping depth on different rake angles. A nonlinear context and an independence of the rake angle from the cutting resistance of wood even at such high rake angles of 35 and 47 were observed. However, a higher rake angle leads to a decrease in the variation of the results especially when cutting lower density wood. Comparing the required chipping force, it is remarkable that the higher density wood of European beech leads to a 2.25 times higher resistance than the lower density spruce. These experimental results act as comparative values for the validation of the simulation. Following the adjustment of the unknown parameters in the numerical material model, a comparably minor deviation is recorded. Future investigations shall focus on the influence of wood exhibiting more moisture than in the presented numerical material model.