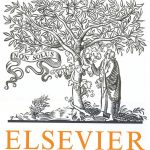
ترجمه مقاله نقش ضروری ارتباطات 6G با چشم انداز صنعت 4.0
- مبلغ: ۸۶,۰۰۰ تومان
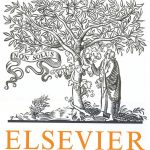
ترجمه مقاله پایداری توسعه شهری، تعدیل ساختار صنعتی و کارایی کاربری زمین
- مبلغ: ۹۱,۰۰۰ تومان
Abstract
Energy and exergy balances were evaluated for the units that constitute the Aromatics plant of a refinery in Portugal (FAR): pre-distillation (Un-0100), Arosolvan (Un-0200), Parex (Un-0300), Isomar (Un-0400) and production of solvents (Un-0500). The FAR had an overall energy yield of 0.81% and an exergetic efficiency of 65.9%. The equipment with higher energy losses, were the condensers, representing 25.9% of the energy losses, followed by air coolers, with 15.4% of the energy losses. The furnaces were in third place with 14.7% of the energy losses. Most of the energy lost in FAR was due to the cooling process. The irreversibilities observed in the condensers and air coolers were equivalent to 1.61% and 0.86% of the total plant irreversibility. Furnaces represent 14.7% of energy losses, but stand out above the irreversibilities analysis with 14.5% of the total. This equipment presents a high potential of energetic and exergetic performance improving, with natural positive impact on energetic and exergetic performance in the FAR. The unaccounted thermal losses represented 32.9% which is mainly justified by the unknown mass flow rate of the gaseous effluent burned in the flare.
6. Conclusions
The presented energy and exergy balances for the aromatics plant of refinery in the north of Portugal show that, even not considering the potential changes on the chemistry of the process, by only analyzing the energy losses and the corresponding exergy destructions, there is a huge potential for the energy utilization through the adequate conversion of the rejected thermal energy. They also demonstrate that the spent energy was essentially used to separate an input low exergy process current into six high exergy different output flows having a relatively high degree of purity. As a main consequence of this analysis some suggestions, although not fully detailed in the present text, were presented to the FAR management. Several of the suggestions concerned good housekeeping procedures like storage tanks isolation, evaluation of the quality and structural integrity of the reactors isolations, analysis of the condensate lines and steam traps. However, the most important suggestions were: – Implementation of an organic Rankine cycle (ORC) to exploit the thermal energy wasted in air coolers; – Implementation of an ORC to exploit the thermal energy wasted from the combustion products of the furnaces; – Implementation of a cogeneration unit producing 11 MW of electrical and 14 MW of thermal energy to supply the FAR. The implementation of the ORC solutions would be non-intrusive because they would simply take profit from the actual situation, by exploiting the large thermal energy wastes available for the production of electricity. By its turn, the implementation of the cogeneration unit would be intrusive as the main furnace of the FAR would be replaced. Through the application of the cogeneration, the energy efficiency of the FAR would increase from the present 0.8–7%, whereas the exergy efficiency would increase from 65.9% to 66.1%. The payback period for this cogeneration unit would be in the range of 2–6 years, depending on the cost of selling electricity to the net and the type of fuel being consumed. The combination of this cogeneration plant with the ORC exploiting the thermal energy wasted from the air coolers would result in the best solution, leading to a further increase of the FAR energy efficiency towards 8.1% and the corresponding exergy efficiency towards 67%. Table 1 represents a summary of the main results for the FAR and its units, and presents also the influence of some of the suggestions to be implemented on the energetic and the exergetic efficiencies of the plant.