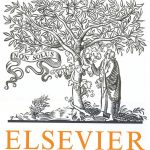
ترجمه مقاله نقش ضروری ارتباطات 6G با چشم انداز صنعت 4.0
- مبلغ: ۸۶,۰۰۰ تومان
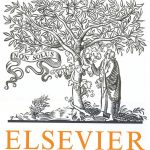
ترجمه مقاله پایداری توسعه شهری، تعدیل ساختار صنعتی و کارایی کاربری زمین
- مبلغ: ۹۱,۰۰۰ تومان
Abstract
The test planning group within Ford's Product Development division develops schedules for building prototype vehicles and assigning them to departments in charge of different vehicle components, systems and aspects (e.g., powertrain, electrical, safety). These departments conduct tests at pre-production phases of each vehicle program (e.g., 2015 Ford Fusion, 2016 Ford Escape) to ensure the vehicles meet all requirements by the time they reach the production phase. Each prototype can cost in excess of $200 K because many of the parts and the prototypes themselves are hand-made and highly customized. Parts needed often require months of lead time, which constrains when vehicle builds can start. That, combined with inflexible deadlines for completing tests on those prototypes introduces significant time pressure, an unavoidable and challenging reality. One way to alleviate time pressure is to build more prototype vehicles; however, this would greatly increase the cost of each program. A more efficient way is to develop test plans with tight schedules that combine multiple tests on vehicles to fully utilize all available time. There are many challenges that need to be overcome in implementing this approach, including complex compatibility relationships between the tests and destructive nature of, e.g., crash tests. We introduce analytical approaches for obtaining efficient schedules to replace the tedious manual scheduling process engineers undertake for each program. Our models and algorithms save test planners' and engineers' time, increases their ability to quickly react to program changes, and save resources by ensuring maximal vehicle utilization.
7. Discussion
In 2012, we piloted our scheduling models and algorithms for the first time on a vehicle program with 108 prototype vehicles budgeted, with an average vehicle cost of around $250 K. The vehicles were scheduled to be delivered starting in May of 2013, at a rate of about 13/week, with a ramp-up period at the beginning. Engineers submitted over 500 test requests. Practically speaking, producing an initial schedule with a utilization of 95%—based exactly on engineer-submitted test requests —exceeded expectations for our initial pilot. To further increase utilization, test planners typically negotiate timing with engineers as schedules are constructed. For example, if 7 days remain unused on one vehicle and the test planner has a 10 day test needing to be scheduled that is otherwise compatible with that vehicle, it may be added by slightly shortening time allocated for each of the tests assigned to that vehicle.