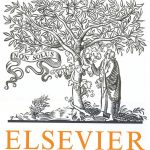
ترجمه مقاله نقش ضروری ارتباطات 6G با چشم انداز صنعت 4.0
- مبلغ: ۸۶,۰۰۰ تومان
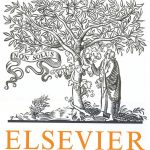
ترجمه مقاله پایداری توسعه شهری، تعدیل ساختار صنعتی و کارایی کاربری زمین
- مبلغ: ۹۱,۰۰۰ تومان
Additive manufacturing AM – 3D printing – is evolving and is currently experiencing its phase of industrialization. Applications are multiple and some are starting to have a real impact on the supply chain. With the use of layer-by-layer additive construction manner, AM changed the way of designing and manufacturing parts. AM technologies are planned to be the core of the next generation of production systems. Still, only few planning and scheduling approaches are proposed in the literature in order to operate AM systems efficiently.
In this work, the planning, nesting and scheduling problem in additive manufacturing is introduced. The aim is to satisfy the orders received from different distributed customers by due dates. The rising interest comes as AM’s reaching a threshold level of maturity and the existing production planning and scheduling approaches have to be adapted and further developed in order to meet the technical and the organizational requirements of the additive manufacturing technologies. The mathematical formulation of the problem is presented, and a heuristic approach is proposed and developed in Python in order to solve it. The proposed heuristic solution is explained step by step, and illustrated using a numerical example. Experimental tests using the proposed heuristic are carried out, underlining the importance of planning/scheduling for an optimized production with AM.
1. Introduction
Additive Manufacturing (AM) is the process of joining materials to make parts from 3D model data layer upon layer as opposed to subtractive manufacturing technologies. Additive manufacturing takes its roots from rapid proto5 typing developed for creating models and prototype parts. Rapid prototyping is known as the first form of creating layer-by-layer a 3D object using ComputerAided Design (CAD) [1]. Additive Manufacturing, and despite its existence for more than three decades, did not gain popularity in industry until very recently. In fact, the recent fast growth rate of AM among industrials and researchers 10 in several fields is proof that it has the potential to be an effective technology for manufacturing components and final products [2]. Based on its maturity in some extent, AM becomes today a main technology in some manufacturing contexts since it can be used in several application fields, especially in customized production [3].
8. Conclusion
In this work, the production planning and scheduling of identical parallel AM machines was considered. Manufacturing orders received from distributed customers were dispersed on a part by part basis using specific due date, height, production area, and volume, then regrouped in a job by job basis in order to be scheduled on the set of given AM machines. The objective was to fulfil the dif- ferent orders by due dates and to minimize the total tardiness, while maximizing machine utilization. To do so, we first reviewed the existing literature related to the topic and found that little research attention is paid to address this research question. However, all pertinent information was gathered and integrated in the solution building mechanism, including the AM processes specifications, existing cost and build time estimation models, nesting methods, and existing scheduling methods and heuristics approaches. After that, we defined and explained the problem characteristics, which differentiates it from the classical machines scheduling problems. Then, we presented the mathematical formulation of the problem and proposed a heuristic procedure in order to solve it. The heuris tic approach was build based on the earliest due date (EDD) rule, developed in Python and explained step by step through some numerical demonstrative cases. In the end, we conducted some experimental tests, showing the need of developing proper additive manufacturing planning and scheduling methods, in order to meet the technical and the organizational requirements of AM.