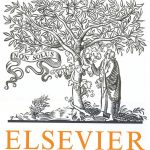
ترجمه مقاله نقش ضروری ارتباطات 6G با چشم انداز صنعت 4.0
- مبلغ: ۸۶,۰۰۰ تومان
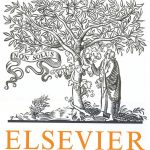
ترجمه مقاله پایداری توسعه شهری، تعدیل ساختار صنعتی و کارایی کاربری زمین
- مبلغ: ۹۱,۰۰۰ تومان
Abstract
The relation of the non-singular opening stress component with apparent fracture toughness was investigated for unidirectional carbon-fiber laminates by means of double cantilever beam experiments in which laminate thickness was varied. It was found that a sample configuration with smaller thickness related to a higher apparent fracture toughness measurement. This result was explained by the presence of a negative non-singular opening stress component, which was found to decrease with thickness. The experimental procedure utilized first crack propagation from the initial polytetrafluoroethylene insert to avoid ambiguity of defining crack location due to crack curving, resulting in a wider crack front and fiber bridging. The two dimensional finite element analyses were used to calculate the corresponding singular and non-singular stress components and the energy release rates. Based on the experimental results a two parameter linear elastic fracture mechanics model was calibrated to incorporate the thickness dependence of the apparent fracture toughness.
5. Conclusions
The thickness dependence of the apparent delamination fracture toughness in laminated unidirectional composites was investigated using DCB specimens of different thicknesses. To avoid the associated discrepancy in the experiment due to crack curving after initial crack propagation from the Teflon film insert and fiber bridging, only the first (initiation) values of fracture toughness were considered. Higher fracture toughness values were found for thinner DCB specimen. To explain such phenomenon, a linear elastic solution was examined to include the second non-singular opening stress component by means of 2D plane-strain finite element analysis. The size of the K-dominant zone was found to be on the same order of magnitude as the sizes of the fracture process zones reported in the literature for the brittle thermosets and thermoplastics. In such a case, the role of the non-singular stress component becomes important. It was found that for the considered DCB thicknesses, the non-singular opening stress component was negative, and its relative magnitude with respect to the singular stress was higher in thinner DCB samples. The amplitude of nonsingular opening stress was calculated from FEA analysis and related to the apparent fracture toughness. The classical LEFM predicts the local fracture event using a single parameter, which describes singular stresses at the crack tip. However, a single parameter criterion provides an incomplete description of the near crack tip stress conditions in the case of interlaminar fracture toughness testing with the DCB specimen configuration. The critical ERR or SIF depend on the structural constraint (thickness) of a DCB test sample, so the single parameter fails to precisely describe the actual full stress field at the vicinity of a crack tip and should be used carefully in order to characterize the fracture behavior of the material. Ignoring the constraint effects can result in a transferability problem of the delamination toughness measured on a laboratory specimen and the integrity assessment of a damage tolerant laminated composite structure. The basic requirement for transferability is that the critical values of the parameters used to characterize singular and non-singular stress components must be the same in a tested specimen and in the actual structural component.