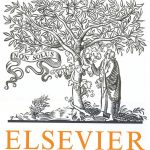
ترجمه مقاله نقش ضروری ارتباطات 6G با چشم انداز صنعت 4.0
- مبلغ: ۸۶,۰۰۰ تومان
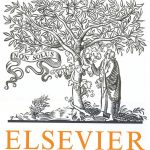
ترجمه مقاله پایداری توسعه شهری، تعدیل ساختار صنعتی و کارایی کاربری زمین
- مبلغ: ۹۱,۰۰۰ تومان
ABSTRACT
Lifetime of wind turbine inverters is below expectations therefore, novel design and drive strategies are timely required to achieve optimum life span. In this work, a novel driving strategy to mitigate stresses on inverters is proposed. First, an electro thermal analysis was carried out using finite element modelling methods. Subsequently, the outcomes of the models were validated using DC/AC IGBT based power inverter module interfaced to 1.1 kW electrical outputs of a horizontal wind turbine operated under different wind speeds. Real time data was collected using both dSPACE system and high speed thermal imaging camera. The proposed driving method is based on adjusting the switching frequency according to wind speed. Edge detection scheme was embedded in Simulink to determine temperature fluctuations caused by variations in wind speed profile. Effects of these fluctuations are mitigated by regulating the switching frequency and power losses based on a look up table and interpolation method. The proposed strategy of operation reduces cyclic temperature depended lifetime span (total lifetime consumption) to 1.45 × 10−5 cycles compared to 1.88 × 10−5 when operated under conventional fixed frequency. Wire-bond thermal stress was also reduced from 54.5 MPa, for the fixed switching frequency, to 45.5 MPa. This represents about 21% reduction in total lifetime consumption of inverter's wire-bond which, brings huge benefits to wind energy industry.
5. Conclusion
An effective driving method, to extend lifetime of DC-AC inverters, have been proposed and experimentally verified. The proposed switching frequency method reduces inverter's wire-bond total lifetime consumption by about 21%. Total lifetime consumption of 1.88 × 10−5 with conventional fixed frequency operation was effectively reduced to 1.45 × 10−5 with the proposed driving method. This has been verified using finite element modelling and data collected from a wind turbine system while working under realistic operating conditions. The total von Mises stress, occurring at the wire-bonds of the inverter, was decreased from 54.5 MPa for the fixed switching frequency to 45.5 MPa with the proposed controlled frequency operation method. The possible drawback for the proposed method could be the visible distortions on the sinusoidal current and voltage signals. These could be minimised by keeping fixed ratio between fundamental and carrier frequencies and can be further eliminated by active filtering methods in further studies. It is believe that the proposed method is now ready to be adopted by industry