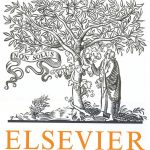
ترجمه مقاله نقش ضروری ارتباطات 6G با چشم انداز صنعت 4.0
- مبلغ: ۸۶,۰۰۰ تومان
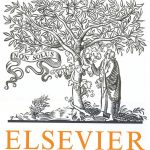
ترجمه مقاله پایداری توسعه شهری، تعدیل ساختار صنعتی و کارایی کاربری زمین
- مبلغ: ۹۱,۰۰۰ تومان
Abstract
The purpose of the presented work was to undertake experimental trials to demonstrate the potential capabilities of a novel in-situ robotic ultrasonic scanning technique for measuring and monitoring loss of the cladding wall thickness in fuel pins of Advanced Gas-cooled Reactors using non-radioactive samples. AGR fuel pins are stainless steel cylindrical ribbed pipes of inner diameter of the rod being about 15 mm and wall thickness of about 300 μm. Spent AGR fuel pins are stored in a water pond and thus may be prone to corrosion and stress-corrosion cracking under adverse conditions. An ultrasonic immersion transducer with central frequency of 25 MHz was used to measure wall thickness of the AGR fuel cladding. The novelty of the approach consists in the usage of a frequency domain technique to measure the wall thickness combined with cylindrical ultrasonic scanning of the samples performed using an industrial robotic manipulator. The frequency domain approach could detect wall thicknesses in the range 96 μm to 700 μm with a resolution of about 10 μm. In addition to the frequency domain measurements, using conventional time domain techniques, it was possible to detect very short (2.5 mm long) and shallow (100 μm in depth) crack-like defects in the fuel cladding.
4. Conclusions
This paper has presented the results of an experimental feasibility study of robotic ultrasonic measurement of the cladding wall thickness of fuel pins of Advanced Gas-cooled Reactor (AGR) for various typologies of defects. It has been demonstrated that it was possible to measure the thickness of AGR fuel cladding, specifically between 96 μm and 700 μm, using a 25 MHz focused ultrasonic immersion transducer by means of the frequency domain approach. It has been experimentally shown that robotic 3D scanning of AGR fuel pins can be implemented with a spatial resolution of 0.25 mm with a linear scan speed not exceeding 20 mm/s. Small (2.5 mm long) and shallow (100 μm in depth) crack-like defects (EDM notches) were detected using time-domain techniques. Robot positional inaccuracy (±1 mm) in the radial direction did not significantly affect the thickness measurement. The angle of deviation of the incident angle of the ultrasonic from normal to the pin surface, at which thickness measurement became erroneous, was found to be 10.8 degrees. This paper represents the first use of 6 axes robotic arm delivery of ultrasonic inspection of AGR fuel cladding. It overcomes traditional challenges with accurate geometric positioning of the ultrasonic immersion transducer and its alignment in comparison to traditional Cartesian axis 3D scanners. The sample’s small wall thickness prevented the use of standard time domain depth measurement; therefore a novel frequency domain technique was developed.