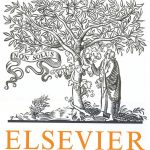
ترجمه مقاله نقش ضروری ارتباطات 6G با چشم انداز صنعت 4.0
- مبلغ: ۸۶,۰۰۰ تومان
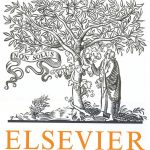
ترجمه مقاله پایداری توسعه شهری، تعدیل ساختار صنعتی و کارایی کاربری زمین
- مبلغ: ۹۱,۰۰۰ تومان
Abstract
Today, fiber reinforced polymer composites are a standard material in applications where a high stiffness and strength are required at minimal weight. Although fiber reinforced polymer composites show many advantages compared to other materials, delamination between reinforcing plies remains a major problem limiting further breakthrough. Previous work has shown that electrospun nanofibers can significantly improve the interlaminar fracture toughness of fiber reinforced composites thus preventing delaminations. In the present paper, the effect of the morphology of the toughening polymer is analyzed by incorporating different polycaprolactone structures in the interlaminar regions. Both Mode I and Mode II interlaminar facture toughness of composites containing five different electrospun morphologies - nanofibers, microfibers, microspheres, dense films, and PCL spray coated glass fibers - were evaluated. Analyzing the fracture behavior of the PCL toughened laminates ensures a better insight in the micromechanical fracture mechanisms behind the observed interlaminar fracture toughness and results in guidelines on the optimal interleave morphology. The results clearly demonstrate the distribution of PCL in the interlayer has a large effect on the crack path of the delamination and the resulting interlaminar fracture toughness. In order to improve the interlaminar fracture toughness in both Mode I as well as Mode II without adverse effects, porous PCL structures such as PCL nanofibers, microfibers, and microspheres are much more suitable than non-porous structures such as PCL films or spray-coated glass fibers. Among the porous structures, the nanofibers had an overall better performance with an increase in Mode I and Mode II interlaminar fracture toughness of about 60% and 80% respectively.
4. Conclusions
The effect of different PCL morphologies on the Mode I and Mode II interlaminar toughness of resin transfer molded glass epoxy laminates was studied. The PCL structures are classified as non-porous (PCL films and spray-coated glass fibers) or (highly) porous structures (PCL nanofibers, microfibers and microspheres). A significant increase in the Mode II fracture toughness requires porous interleave structures. These structures have an intense fine distribution of PCL phases in a surrounding epoxy phase allowing for the PCL to strain significantly when the epoxy surrounding is cracked. The use of highly porous PCL nanofibers gave the best result. The non-porous structures could not increase the Mode II fracture toughness since they are not strained significantly during Mode II loading. As for the Mode I fracture toughness, the nonporous structures did allow for an important increase in fracture toughness. This is however combined with an expected detrimental effect on the overall mechanical properties of the composite such as the shear strength, bending stiffness and creep resistance of the laminate due to the low tensile strength and stiffness of the dense PCL interlayer. In addition the non-porous structures obstruct an optimal infusion process and are thus not suitable. In contrast the porous structures show a more interesting Mode I fracture behavior, where interlaminar crossings of the crack path allow for an interaction with the finely distributed PCL phases in the surrounding epoxy phase, again resulting in an increased Mode I interlaminar fracture toughness. For the porous interleave structures the fine distribution and intense blend of PCL and epoxy phases ensures the overall mechanical properties of the composites. Concluding as to improve the interlaminar fracture toughness in both Mode I as well as Mode II without adverse effects, porous PCL structures are much more suitable compared to the non-porous PCL films or spray-coated fibers, with nanofiber interleaving structures showing the best performance. The nanofiber structures allow for a straightforward method to introduce a fine distribution of the PCL phase in the epoxy matrix without the need for a complex separation process.