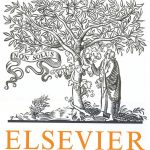
ترجمه مقاله نقش ضروری ارتباطات 6G با چشم انداز صنعت 4.0
- مبلغ: ۸۶,۰۰۰ تومان
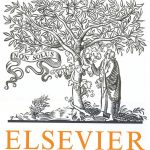
ترجمه مقاله پایداری توسعه شهری، تعدیل ساختار صنعتی و کارایی کاربری زمین
- مبلغ: ۹۱,۰۰۰ تومان
Abstract
In the practical design of nuclear building structures subjected to an aircraft crash, the structures are required to prevent scabbing and perforation. NEI 07-13 provided the formulas to predict the minimum reinforced concrete (RC) wall thickness to prevent the local damage caused by aircraft engine impact. However, these formulas may not be suitable for predicting the thickness of the ultra-high performance fiber reinforced concrete (UHPFRC) wall. In this study, the local damage of a UHPFRC wall caused by the impact of aircraft engine missile is investigated using a finite element program LS-DYNA. The structural components of the UHPFRC panel, aircraft engine model, and their contacts are fully modeled. The analysis results are verified with the test results. A parametric study with varying panel thickness, fiber type and content, and impact velocity is performed to investigate the local damage of the UHPFRC panel. Based on a comparison with the given formulas, the modified equations of Chang and Degen are proposed to predict the minimum wall thickness to prevent scabbing and perforation in the case in which the UHPFRC structure is used.
6. Summary
A systematic approach to the development of an innovative connection between FRP deck panels is presented in this paper. This approach was based on close collaboration between the bridge owner, contractor, manufacturer and designer. Collaborative work was essential in the development of the connection, as it addressed different aspects of the product. Not only the primary functionality of the connection but also the productivity, buildability and serviceability were taken into account. In addition, a new way of thinking by introducing the ‘design for manufacture and assembly’ (DFMA) concept was embraced. The concept of DFMA helped in setting design requirements for the development of the connection. In this way, several innovative connection concepts focusing on meeting the requirements of all parties were proposed. Afterwards, the developed connections were evaluated by means of matrices which were developed specifically for the purpose of this work. After evaluation, the winning connection concept was designed in detail and it was produced for experimental investigation. The advantages of the developed innovative panel level connection in this study are: a) it avoids the need to execute bonding operations on site; ii) it allows for more rapid installation; and iii) it makes the disassembly of bridge panels possible. After manufacturing, the connection was proven to be effective with regard to rapid assembly, which translates into a substantial reduction in total on-site construction time. The test demonstrated that the developed connection meets the stiffness and strength requirements. Slightly ductile behaviour was observed from the load-deflection curves. The results of this study show that the proposed connection has good potential to be used for FRP decks. This, in turn, proves the efficiency of the followed approach for the development of the connection in this paper. Moreover, it supports the need for collaborative working to deliver innovative technology solutions. This methodology can also be used for developing other products than connections.