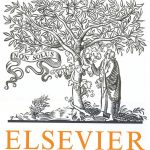
ترجمه مقاله نقش ضروری ارتباطات 6G با چشم انداز صنعت 4.0
- مبلغ: ۸۶,۰۰۰ تومان
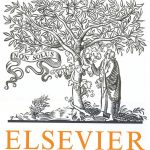
ترجمه مقاله پایداری توسعه شهری، تعدیل ساختار صنعتی و کارایی کاربری زمین
- مبلغ: ۹۱,۰۰۰ تومان
Abstract
Multilevel hierarchical structures built up from nanoscale to macroscale are common in nature, but their potential has not been achieved by man-made composites. The presented multilevel structure consists of carbon nanotube fibers (CNTFs) embedded in epoxy matrix. This structure exploits the supreme mechanical properties of individual CNTs together with the manageability of the microscale CNTFs, and has the potential to overcome the implementation difficulties associated with nanocomposites. Using different chemical treatments (ethylene glycol or nitric acid solvents), the CNTFs are densified and the amount of epoxy penetration inside the CNTFs is controlled, creating an interphase between the single CNTs. The strength and adhesion properties of individual CNTFs in epoxy are measured by continuously monitored fragmentation tests and characterized by electron microscopy. A modified Cottrell-Kelly-Tyson model is applied to account for the CNTF unique cross-sectional geometry, comprising millions of individual multiwalled CNTs, and for the effect of matrix penetration. The composite strength and toughness are found to be strongly dependent on and improved by the extent of penetration, suggesting that the composite mechanical properties would be tunable by controlling the interphase. The presented integrative analysis shows that CNTF based composites are an excellent potential choice for strong and tough structures, as well as for bio-engineering.
4. Conclusions
A multilevel composite structure is presented, consisting of CNT fibers embedded in epoxy matrix. The proposed composite bears resemblance to a tendon as it has a similar structural hierarchy, is self-assembled from nanoscale to macroscale, and is simultaneously strong and tough, a combination rarely found in engineering materials. While such structures are common in nature, implementation difficulties impede their realization in man-made composites. By tailoring advanced experimental and theoretical techniques, we show how the degree of polymer penetration inside the CNTF can be controlled, thereby boosting the composite structural toughness and, at the same time, achieving the supreme strength owed to carbon nanotubes. The use of CNTFs as reinforcing fillers in composites bridges the gap between nanoscale and macroscale, so perfectly realized in multi-level hierarchical biological structures. CNTFs combine the excellent mechanical properties of CNTs with the handling ease of microsized fibers. By way of surface treatment, CNTFs can be densified to a desired compactness, enabling the control of the amount of matrix penetration, an interphase, during composite preparation. The composite structure comprises four hierarchical levels from nanoscale to macroscale - individual CNTs, CNT bundles, CNTFs, and composite e allowing the tuning of the composite mechanical properties to desired strength, stiffness and toughness. We demonstrate how the amount of interphase can be controlled by applying chemical treatments to the CNTFs. Fragmentation tests are used to characterize the strength of CNTFs in epoxy and the CNTF-epoxy interfacial strength. A highly densifying treatment, using HNO3 as solvent, results in minimal polymer penetration into the CNTF. By contrast, a less densifying treatment, using EG as solvent, results in substantial penetration, and creation of an interphase that effectively strengthens the CNTF-matrix interface. The effective CNTF tensile and interfacial strengths, as well as the fracture behavior, are found to be greatly influenced by the amount of interphase, which is therefore key to the composite performance. Our theoretical analysis shows that both the strength and toughness of a composite reinforced by CNTFs are potentially an order of magnitude higher than those achievable with uniformly dispersed aligned CNTs. This observation is particularly interesting and somewhat paradoxical in view of the much higher material strength of an individual CNT compared to an individual CNTF, and it echoes a general observation on natural structures in which the strength is graded from very strong components at the lowest level (nano scale) to weaker sub-structures at the higher level (micro and macro scales). Furthermore, the toughness of a CNTF reinforced composite can be increased significantly by creating an interphase, mainly because additional pullout energy is absorbed inside the CNTF, but also because an interphase helps arresting and diverting cracks propagation. The enhanced toughness seems to be a critical advantage of CNTF reinforcement over CF reinforcement. A modi- fied (generalized) filler-failure CKT model is presented to better account for the CNTF complex internal structure including voids and interphase, amounting to about double the interfacial area in the EG treated CNTF compared to the HNO3 treated CNTF. These preliminary results should be expanded in future research by exploring additional methods for tuning the interphase, so as to clarify the role of matrix penetration in the composite mechanical performance. Such tuning could be done by, for example, using polymer solutions with different viscosities, impregnating CNTFs with a softer polymer, treating CNTFs to achieve various levels of density, and applying different vacuum/temperature/time conditions to control the penetration process. Further exploration should also address implementation of CNTF based composites in applications requiring strong and tough structures, as well as in bioengineering.