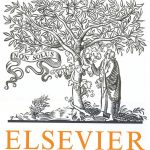
ترجمه مقاله نقش ضروری ارتباطات 6G با چشم انداز صنعت 4.0
- مبلغ: ۸۶,۰۰۰ تومان
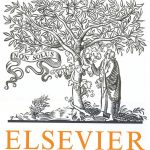
ترجمه مقاله پایداری توسعه شهری، تعدیل ساختار صنعتی و کارایی کاربری زمین
- مبلغ: ۹۱,۰۰۰ تومان
ABSTRACT
Advanced composite structural components in aeronautics are characterized by very high production costs because of their dimensions, complex shapes and expensive forming equipment. For these components, such as horizontal stabilizers and wings, a defect occurrence is often critical because large part of inner surfaces, made of long and tapered narrow tunnels, are not reachable for repair operations. In these cases, the part is rejected with a relevant economic loss and high production costs. For this reason, aircraft constructors plan huge investments for defects avoidance during the forming processes of CFRP and to develop effective, robust and reliable repair tools and methods. Mobile robotics can play an important role, with specific systems capable of moving into narrow channels of wings structures (i.e. multi spar boxes) and repair it in accordance to technical standards. This paper describes an innovative mobile robot architecture for bonded repair scarfing operations on CFRP components. Targeting and responding to the demanding machining requirements, the functional-oriented design approach clearly highlights the advantages of a modular robotic solution. The mobile robotic architecture can be also applied in other fields with similar challenging manufacturing operations for further inspection, detection and machining operations.
8. Conclusions
In the present work, the issue of repairing internal damages or manufacturing defects affecting a specific group of aeronautical components is addressed. The topic is particularly relevant, due to the lack of existing solutions: manual scarfing and application of repair plies, indeed, cannot be performed in the majority of the cases, due to the inaccessibility of the defected zone. A semi-autonomous scarfing mobile system concept is proposed, and its feasibility is demonstrated. A mobile robotic system aimed to such machining operations must be capable of the required performance complying with the challenging geometrical and technological constraints. Due to this, several existing robotic solutions for demanding applications in confined spaces have been analyzed, and the most suitable strategies (i.e. the implementation of pushers for spatial stability inside tunnels) are taken into account. With these hypotheses, starting with the definition of all system requirements and aiming to an optimized solution, the present study is based on a task-oriented approach. The proposed concept is composed by a multi-purpose mobile modular architecture (Rover and Semi-trailer), two interchangeable tools (Scarfing and Cleaning Forearms), and an articulated interface to equip them with the necessary mobility (Arm). The rover module is ready to host a specifically designed structured-light 3D scanner and a “Ply Application Forearm” would complete the robotic set to perform all the on-site operations. A control strategy is proposed to match two main requirements: 1) automatize some stages of the repair process (3D geometry reconstruction, positioning, toolpath calculation, scarfing, solvent deposition, etc.); 2) allow expert operators to supervise and monitor the operation and meet the required quality of the repair. In the Discussion section, some critical aspects are deepened, validating the concept design: compliance of the architecture with the requirements, machining functionalities and design of the Arm. This study represents a step towards the automated repairing of internal inaccessible zones of aircraft components, proposing a novel solution based on a mobile robotic system.