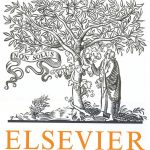
ترجمه مقاله نقش ضروری ارتباطات 6G با چشم انداز صنعت 4.0
- مبلغ: ۸۶,۰۰۰ تومان
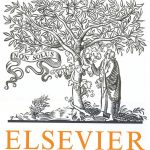
ترجمه مقاله پایداری توسعه شهری، تعدیل ساختار صنعتی و کارایی کاربری زمین
- مبلغ: ۹۱,۰۰۰ تومان
Abstract
Lean manufacturing is a production method that was established in the wake of the Japanese Toyota Production System and rapidly established in the worldwide manufacturing industry. Lean characteristics combine just-in-time practices, work-in-progress and waste reduction, improvement strategies, defect-free production, and standardization. The primary goal of lean thinking is to improve profits and create value by minimizing waste. This study introduces a novel mathematical model to design lean processes in hybrid assembly lines. The aim was to provide an effective, efficient assembly line design tool that meets the lean principles and ergonomic requirements of safe assembly work. Given the production requirements, product characteristics and assembly tasks, the model defines the assembly process for hybrid assembly lines with both manual workers and automated assembly machines. Each assembly line solution ensures an acceptable risk level of repetitive movements, as required by current law. This model helps managers and practitioners to design hybrid assembly lines with both manual workers and automated assembly machines. The model was tested in a case study of an assembly line for hard shell tool cases. Results show that worker ergonomics is a key parameter of the assembly process design, as other lean manufacturing parameters, e.g. takt time, cycle time and work in progress.
6. Conclusions
Lean manufacturing is a production strategy that is used to increase profit by eliminating waste. After the success of the Japanese Toyota Production System in the 1980s, lean manufacturing was rapidly established in the worldwide manufacturing industry. Despite the promising results in the economic performances of some companies, recent studies have shown a potential correlation be wee pec c e p c ce w ke ’ e g m c , ccup he h e e k factors. However, automation plays a strategic role in increasing productivity and reducing the production time in manufacturing companies. Further reasons to automate the manufacturing processes include the presence of hazardous working conditions and the high cost of specialized manual workers. The current market requires companies to find a balance between the advantages of automated production and the dynamic demand for customized products. When automation cannot provide great flexibility, production system design requires the joint optimization of human and technical aspects.
This paper addresses the design of hybrid assembly lines, fulfilling the principles of lean manufacturing and the ergonomic requirements for safe assembly work. A bi-objective integer linear programming mathematical model drives the choice between manual and automatic workstations. The primary assumption is the design of hybrid lean processes that avoid the machine pacing of workers and the related harmful effects. Given the production requirements and characteristics of the work system, the result is a set of worker-paced hybrid assembly line solutions. The model defines the sequences of manual and automatic workstations, in which the machine pace is set by the manual workstations. Furthermore, each assembly line solution ensures an acceptable risk level of repetitive movements, as required by current law. The case study introduces the application of the proposed mathematical model to an assembly line. The aim is to investigate the impact of ergonomics on the lean manufacturing process. Results show that worker ergonomics is a key parameter of the assembly process design, as other lean manufacturing parameters, e.g. takt time, cycle time and work in progress. The model includes the OCRA risk assessment, as required by the Italian regulations on occupational safety. Specifically, the mathematical model restricts the OCRA index value to a threshold limit value for each task (ISO 11228-3, 2007). The choice of a different ergonomic risk assessment method might produce different results and have a substantial impact on the design of hybrid assembly lines. Future developments of this work include the adoption of a different ergonomic risk assessment method and the analysis of the impact on the solutions of model. Finally, the proposed mathematical model will be tested on complex assembly lines with no sequential workstations.