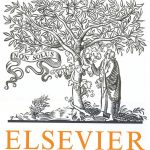
ترجمه مقاله نقش ضروری ارتباطات 6G با چشم انداز صنعت 4.0
- مبلغ: ۸۶,۰۰۰ تومان
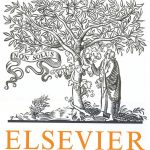
ترجمه مقاله پایداری توسعه شهری، تعدیل ساختار صنعتی و کارایی کاربری زمین
- مبلغ: ۹۱,۰۰۰ تومان
abstract
In this paper, the behaviour of concrete filled tubular flange girders (CFTFGs) is investigated through both numerical and analytical modelling. These are new and complex members and their behaviour is governed by a number of inter-related parameters. This work aims to study the relative influence of a number of these variables on the flexural behaviour, particularly for CFTFGs with stiffened webs. A nonlinear three-dimensional finite element (FE) model is developed in the ABAQUS software and is validated using available experimental data. The validated model is then employed to conduct parametric studies and investigate the influence of the most salient parameters. For comparison purposes, and to observe the effect of the concrete infill, steel tubular flange girders (STFGs) with a hollow flange are also studied. The finite element models consider the effects of initial geometric imperfections, as well as other geometrical and material nonlinearities, on the response. In addition, simplified analytical expressions for the flexural capacity are proposed, and the results are compared to those from the FE analyses. It is found that CFTFGs and STFGs with the same dimensions have similar buckling shapes but different buckling loads, with the CFTFG offering greater buckling resistance. This highlights the influence of the concrete infill which increases the stiffness of the upper flange, and hence allows the member to carry additional bending moments compared to STFGs. The proposed analytical expressions, which are suitable for design, are also shown to be capable of providing an accurate depiction of the behaviour and bending moment capacity.
Conclusions
This paper has presented a detailed investigation in the behaviour of concrete filled tubular flange girders (CFTFGs) under bending. In the absence of significant experimental testing in the literature, a finite element model was developed using the ABAQUS software [16] to study the response and also the relative influence of the most salient parameters. The accuracy of the FE models was initially assessed using the experimental results of Wang et al. [15], who conducted the only test on these members in the public domain, and it was shown that the proposed FE model is able to provide a very good prediction of the general behaviour and the ultimate capacity. In addition to the numerical model, an analytical model was also developed and discussed, which predicts the bending capacity of these members based on a plastic analysis approach. The analytical approach was validated using both the experimental data available as well as the FE model. Thereafter, parametric studies were conducted to study the relative influence of several key parameters including the size of the tube diameter (Dtube), the ratio of Dtube to the tube thickness, the thickness of the bottom flange, the web plate slenderness, the aspect ratio of the web panel and also the material strengths. Ultimate moment versus vertical deflection curves and failure modes were obtained from the analyses.