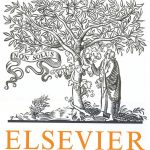
ترجمه مقاله نقش ضروری ارتباطات 6G با چشم انداز صنعت 4.0
- مبلغ: ۸۶,۰۰۰ تومان
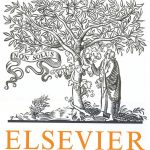
ترجمه مقاله پایداری توسعه شهری، تعدیل ساختار صنعتی و کارایی کاربری زمین
- مبلغ: ۹۱,۰۰۰ تومان
ABSTRACT
A peculiar type of edge discoloration defect on the surface of some galvanized fuel tank was observed, causing significant appearance problems. In the present study, the surface defect was characterized by visual inspection, optical microscopy, scanning electron microscopy and energy dispersive spectroscopic analysis to understand the source and mechanism of the defect. In the visual inspection, these peculiar surface appearances were observed in fuel tank at three distinct locations. The SEM examination exhibited two distinct regions on the surface apart from the normal galvanized surface: (1) galvannealed, (2) mixture of galvanized and galvannealed texture. The energy dispersive spectroscopic analysis of galvannealed region indicated enrichment of Zn and Al whereas in the region of galvanized majorly Zn was observed. Surface texture of galvannealed region showed majorly zeta crystals along with skin pass marks; whereas no such zeta crystals were observed in case of galvanized regions. Based on the preliminary results, the following hypothesis was made: Coil processed during galvanizing to galvannealing transition. Thickness and width changed to wider and thicker section, which resulted into lower line speed. Due to the lower Al content, lower speed and thicker section combination resulted in formation of partial GA in the coil owing to the internal heat content of the coil. This paper presents the results of the investigation.
5. Conclusion
Due to lower bath aluminium content(0.13% as compared to 0.185 regular during galvanizing process), lower speed and thicker section combination resulted in formation of partial Galvannealed surface in the coil owing to the internal heat content of the coil. It is recommended that coils for automotive galvanizing grade are not to be scheduled during unstable zinc condition (like run down).