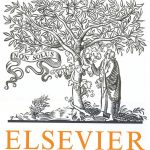
ترجمه مقاله نقش ضروری ارتباطات 6G با چشم انداز صنعت 4.0
- مبلغ: ۸۶,۰۰۰ تومان
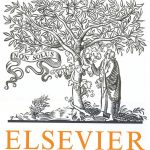
ترجمه مقاله پایداری توسعه شهری، تعدیل ساختار صنعتی و کارایی کاربری زمین
- مبلغ: ۹۱,۰۰۰ تومان
Abstract
Design of large composite structures requires understanding the scaling of their mechanical properties, an aspect often overlooked in the literature on composites. This contribution analyzes, experimentally and numerically, the intra-laminar size effect of textile composite structures. Test results of geometrically similar Single Edge Notched specimens made of [0∘]8 epoxy/carbon twill 2 × 2 laminates are reported. Results show that the nominal strength decreases with increasing specimen size and that the experimental data can be fitted well by Bažant's size effect law, allowing an accurate identification of the intra-laminar fracture energy of the material, Gf. The importance of an accurate estimation of Gf in situations where intra-laminar fracturing is the main energy dissipation mechanism is clarified by studying numerically its effect on crashworthiness of composite tubes. Simulations demonstrate that, for the analyzed geometry, a decrease of the fracture energy to 50% of the measured value corresponds to an almost 42% decrease in plateau crushing load. Further, assuming a vertical stress drop after the peak, a typical assumption of strength-based constitutive laws implemented in most commercial Finite Element codes, results in an strength underestimation of the order of 70%. The main conclusion of this study is that measuring accurately fracture energy and modeling correctly the fracturing behavior of textile composites, including their quasi-brittleness, is key. This can be accomplished neither by strength- or strain-based approaches, which neglect size effect, nor by LEFM which does not account for the finiteness of the Fracture Process Zone.
5. Conclusions
This paper presents and discusses an experimental and numerical investigation on the intra-laminar size effect of textile composites. Based on the results presented in this study, the following conclusions can be formulated: 1. The experimental investigation shows a remarkable size effect in geometrically-scaled textile composite structures failing by intra-laminar fracture propagation. This aspect, too often overlooked in the literature on composites, is the determining factor for damage tolerance design of large composite structures; 2. The tests agree with Size Effect Law (SEL) proposed by Bazant [4,24], according to which the fracturing behavior of geometrically scaled structures exhibits a smooth transition from ductile to purely brittle (LEFM type) with increasing structure size; 3. Size effect tests can be used to determine the fracture characteristics of the composite provided that a) the orthotropic properties of the material are taken into account and b) realistic boundary conditions are assumed for the calculation of the dimensionless energy release rate. The size effect method of measuring the fracture properties is easier to implement than other methods because only peak load measurements are necessary: the post-peak behavior, crack tip displacement measurement and optical measurement of crack tip location are not needed, and even a soft testing machine without servocontrol can be used. According to this approach, the initial fracture energy Gf of the investigated carbon twill 2 2 composite was identified to be 73.7 N/mm whereas the effective Fracture Process Zone (FPZ) length, cf was 1.81 mm. This length is comparable to the size of one tow; 4. The applicability of SEL to measure the fracture properties of the material was verified numerically by means of two recently proposed microplane models for textile composites [9e11]. Both formulations matched the size effect data using the Gf-value estimated by SEL; 5. Compared to the experimental results on the axial progressive crushing behavior of composite crush cans, the models calibrated with the measured fracture energy provided an excellent prediction of the crushing load. Further, a parametric study showed that, for both models, a decrease of Gf to about 50% of the measured value can reduce the crushing load to almost a half. The assumption of a vertical drop of the stress after the peak, typical of strength-based constitutive laws, resulted into an underestimation of the order of 70% for an element size of 2 mm. The error in this latter case is mesh dependent; 6. The foregoing results suggest that measuring accurately Gf and modeling correctly the fracturing of textile composites, including their quasi-brittleness, is the key in all situations which require accurate prediction of energy absorption (such as crashworthiness analysis) or scaling of mechanical properties. This can be accomplished neither by strength-based approaches, which completely neglect the size effect, nor by LEFM, which does not account for the finiteness of the FPZ.