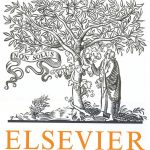
ترجمه مقاله نقش ضروری ارتباطات 6G با چشم انداز صنعت 4.0
- مبلغ: ۸۶,۰۰۰ تومان
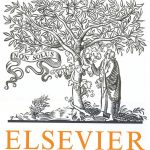
ترجمه مقاله پایداری توسعه شهری، تعدیل ساختار صنعتی و کارایی کاربری زمین
- مبلغ: ۹۱,۰۰۰ تومان
Abstract
Earthwork equipment accounts for a large proportion of the fatalities on construction sites. According to the U.S. Bureau of Labor Statistics, in the period between 1992 and 2002, struck by vehicles and struck by objects (e.g., vehicle parts, vehicle loads, or falling vehicles) were identified as the causes of 30% and 24% of fatal equipment-related accidents on excavations sites, respectively. It is therefore of a paramount importance to improve the safety of construction sites by increasing the peripheral awareness of the operators of earthwork equipment. Several research works have investigated numerous collision avoidance systems that exploit real-time location systems and proximity measurements to mitigate the risk of accidents on excavation sites. However, these systems often detect collisions based on using the workspaces that only account for the geometry and the degrees of freedom of the equipment, and thus disregard the state-dependent characteristics of equipment. This results in reserving a large space for every piece of equipment, which reduces the applicability of these systems in congested sites. Therefore, this paper proposes a novel method for generating dynamic equipment workspaces based on the continuous monitoring of a spectrum of equipment-related information, i.e., the current pose/state of the equipment, and the speed characteristics of each movement. This method uses the required operation stoppage time to determine how much space needs to be reserved for each piece of equipment. A case study is conducted to validate the proposed method. It is shown that the proposed method has a strong potential in capturing the hazardous areas around the equipment and triggering warnings in view of the impending movements of various pieces of equipment. Also, the proposed method proved to have potential applications in actual projects in congested sites where space is limited.
6. Conclusions and future work
This paper proposed a novel method for the generation of realtime dynamic equipment workspaces considering the pose, state, geometry, and the speed characteristics of the equipment. This method is built on the previous work of the authors, where robust methods for the calculation of pose and state of different pieces of equipment based on RTLS data were presented. The present method considers the required operator stoppage time to determine how much space needs to be reserved in order to ensure that the equipment will not collide with other pieces of equipment in the immediate future. Excavators and trucks were used as the representatives of different types of equipment used in an earthwork project. The appropriate DEWs and their calculation process for all possible states of the equipment were presented. Finally, the application of DEWs for the calculation of congestion index was discussed. In view of the results of the case study, it can be concluded that: (1) the proposed method is providing a balance between economic use of space and the ability to warn against potential collisions in an effective manner using the pose, state, geometry, and speed characteristics of the equipment, (2) the flexibility of the method in using more than one speed vector in the calculation of DEWs enabled effective capturing of the operation of skilled operators where multiple DOFs can be used simultaneously. Finally, some false warnings resulted from capturing the movement along various DOFs only in 2D. Therefore, the future efforts of the authors are dedicated to avoiding this problem by considering the details of the movement in the third dimension in the generation of DEWs. Also, the authors plan to conduct a test on a construction site where the UWB system can be tested under the actual site conditions.