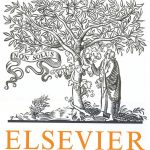
ترجمه مقاله نقش ضروری ارتباطات 6G با چشم انداز صنعت 4.0
- مبلغ: ۸۶,۰۰۰ تومان
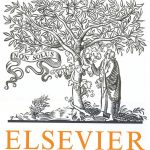
ترجمه مقاله پایداری توسعه شهری، تعدیل ساختار صنعتی و کارایی کاربری زمین
- مبلغ: ۹۱,۰۰۰ تومان
Abstract
This paper deals with the simulation of multiple crack propagation in friction stir welded butt joints and the aim is to assess the influence of process induced residual stresses on the fatigue behavior of the assembly. The distribution of the process induced residual stresses is mapped by means of the contour method; then, the computed residual stress field is superimposed, in the DBEM environment, to the stress field due to a remote fatigue traction load and the crack growth is simulated. A two-parameters crack growth law is used for the crack propagation rate assessment. The Stress Intensity Factors are evaluated by the J-integral technique. Computational results have been compared with experimental data, provided by constant amplitude crack propagation tests on welded samples, showing the subdivision of the overall fatigue life in the two periods of crack initiation and crack propagation.
5. Conclusions
The following conclusions can be highlighted: - the implemented FEM-DBEM approach can be considered as a powerful tool to predict the crack growth in presence of residual stresses induced by manufacturing processes; - if the initial crack starts from the weld line the process induced opening stresses play an accelerating effect on the crack propagation; - the crack propagation provided by the experimental test, characterized by pure mode I evolution and nearly symmetric shape (with respect to the weld line mid plane) qualitatively confirmed the residual stress numerical scenario; - from a post mortem metallographic analysis the initial defect was clearly pointed out, allowing the definition of a realistic initial crack scenario for the numerical simulation; consequently a realistic assessment was provided for the crack propagation fraction of the overall fatigue life; - the absence of crack propagation of the lateral crack coming out from the numerical simulation is consistent with the experimental outcome; - the specimen failure, due to fracture instability, predicted by the numerical analysis when the crack is on the verge to cut through the thickness is consistent with post mortem metallographic analysis of the fracture section.