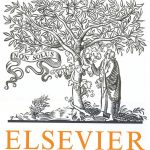
ترجمه مقاله نقش ضروری ارتباطات 6G با چشم انداز صنعت 4.0
- مبلغ: ۸۶,۰۰۰ تومان
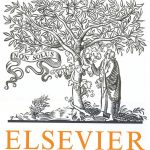
ترجمه مقاله پایداری توسعه شهری، تعدیل ساختار صنعتی و کارایی کاربری زمین
- مبلغ: ۹۱,۰۰۰ تومان
Abstract
Uncertainties in current empirical models for the convective heat transfer coefficient (CHTC) have large impact on the accuracy of building energy simulations (BES). These models are often based on measurements of the CHTC, using a heated gradient sensor, where steady-state convective air flow is assumed. If this requirement is not fulfilled there will be a dynamic measurement error. The objectives were to construct a validated dynamic model for the heated gradient sensor, and to use this model to improve accuracy by suggesting changes in sensor design and operating procedure. The linear thermal network model included three state-space variables, selected as the temperatures of the three layers of the heated gradient sensor. Predictions of the major time constant and temperature time evolution were in acceptable agreement with experimental results obtained from step-response experiments. Model simulations and experiments showed that the sensor time constant increases with decreasing CHTC value, which means that the sensor response time is at maximum under free convection conditions. Under free convection, the surface heat transfer resistance is at maximum, which cause enhanced heat loss through the sensor insulation layer. Guidelines are given for selection of sampling frequency, and for evaluation of dynamic measurement errors.
4.7. System design and operating conditions
Decrease of the system time constant leads to reduction in dynamic errors, which means that higher frequency variations in hc could be measured, without violation of the method requirement to measure under steady-state conditions. With our sensor design, the lower limit for the system time constant is set by the HFM and the PRT sensors used, which have time constants equal to 3 and 2 min, respectively (the latter was experimentally estimated). The time constant for temperature measurement could be reduced down to the seconds-level by replacing the PRT with, for examples, thermocouples or a thermal camera. However, the temperature accuracy may suffer by such actions. The contribution of the HFM to the system time constant could be eliminated by simply removing the HFM from the design, and instead measure the conductive heat flux as the electrically supplied power. This requires, of course, that heat loss through the insulation layer is negligible for all operating conditions. We have seen that heat loss may occur when the sensor is operated under free convection conditions. As shown above, for a given sensor time constant τ (depends on hc), it is required that the sampling frequency is selected to be fs≤1/ 5( τ), in order to fully utilize the sensors capacity to accurately measure the varying hc quantity. The first measurement should be acquired after a waiting time of at least five time constants, in order to reduce the settling error. If there is a constant rate of change in the hc-value in a series of measurements, then this rate of change should be estimated, and used for correction of the lag error.